White Yeti - 16-11-2012 at 19:25
When one prepares glassware for reflux, the condenser is conventionally filled with cooling water from bottom to top. As many of you know, this is
done to avoid trapping bubbles inside the condenser and water pump. However when water flows this way, it flows concurrently with the distillate. This
is perhaps not the most efficient use of a condenser; countercurrent flow would allow for a more efficient heat exchange, at least in theory.
The idea in this case, is to fill the condenser with cooling water from bottom to top, and then reverse the pumping direction once the condenser is
full. This would only apply in reflux scenarios because the water already flows countercurrently to the distillate in simple distillation.
I'm a noob, I don't own a distillation apparatus so I can't try this out myself. I was wondering if any of you have tried this, and if so, if the
efficiency of the condenser increases, or if it remains the same. I also hypothesize that countercurrent flow would decrease strain on glassware,
possibly prolonging the service life of water cooled condensers.
Any thoughts?
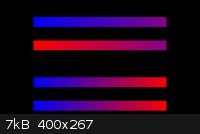
Natures Natrium - 16-11-2012 at 20:05
For whatever its worth, I have always ran my water counter-current in a condenser, regardless of application. During a reflux, when the condenser is
vertical, it has been my experience that the flowing water will chase air bubbles out of the condenser within a minute or two of operation. Should a
tiny bubble remain at the top, it seems like it would be of little importance, as any uncondensed target gas that reaches that level is likely to
escape whether the bubble is there or not.
gsd - 17-11-2012 at 00:23
The key words here are "In Theory atleast".
In practice in 99.9 % of cases it will not matter for following reasons:
1) Normally the water flow rate is very high compaired to the flow of condensing vapours. This is confirmed by very little increase in outlet
temperature of water.
2) Condensation of vapours is an isothermal process. So strictly for condensation there is no co-current or counter-current flow. It is the
sub-cooling of the condensate for which the flow regime becomes relevent, and in case of vertical reflux condenser, with water inlet at the bottom, it
becomes counter-current flow.
The measure of true counter-current flow is a factor called LMTD - Log Mean Temperature Difference. (A cursory reading of any Chem Engg text on Heat
Transfer will explain it)
If the temp change in cooling water is not significant by reversing the flow, then the LMTD hardly changes which means there is no great advantage in
the counterflow arrangement.
Gsd
White Yeti - 17-11-2012 at 07:57
Ok, that makes sense, thanks for the reply.
blogfast25 - 17-11-2012 at 08:33
Despite the occasional heated discussion between amateur distillers on whether to use counter current cooling or not, 'gsd' nails it perfectly: when
cooling water’s temperature is hardly affected by the heat exchange it matters not one jot what sense the water is flowing in.
The LMTD is a very useful concept in engineering where trying to save water (and cost) for large heating exchange operations becomes far more
important.
Endimion17 - 17-11-2012 at 08:53
Yeah, the difference is not important in usual laboratory applications. As long as the reflux ring is below 1/3 of jacket height, it's ok. Never let
that ring climb over that mark because if you're doing a reaction, and there's a sudden spike of released energy, the fumes can quickly climb out and
that usually means trouble.
There's no advantage of any ring height in reflux operations. If you can keep it at the begining of the jacket, that's great. It's not a fractional
distillation where those things matter.
[Edited on 17-11-2012 by Endimion17]
gsd - 17-11-2012 at 09:09
Reversing the flow direction of cooling water in jacket will hardly change the position of reflux ring - Increasing the flow rate most certainly will.
All said and done laboratory glass condensers - especially single surface type - are extremely inefficient heat transfer devices. Three factors which
keep them in business are 1) their ability to handle almost any medium on either side 2) The visibility they provide and 3) ease of cleaning.
gsd