Pages:
1
2
3
4
5 |
JJay
International Hazard
   
Posts: 3440
Registered: 15-10-2015
Member Is Offline
|
|
I don't know much about that fan.... I've been putting a 2'x4'x4' enclosure together for my hood and am super tempted to use a box fan for
ventilation. I am going to use vinyl for the sash (at least initially) since it is cheap, easy to work with, fairly chemically resistant, and hard to
ignite. But in a perfect world I'd build it out of fiber-reinforced concrete panels with a squirrel cage fan and a glass/polycarbonate laminate sash.
[Edited on 20-7-2017 by JJay]
|
|
Geocachmaster
Hazard to Others
 
Posts: 146
Registered: 5-3-2016
Location: Maine, USA
Member Is Offline
Mood: Corroded, just like my spatulas
|
|
I just ordered the 460 CFM version of that fan, zts. It's supposed to arrive on Saturday and I should get my fume hood built this weekend. The plan is
4 feet long, 42 inches high on the inside. My dad is actually a carpenter so it should be built pretty well. 
When it gets done I'll post pictures here and tell you how the fan is.
|
|
JJay
International Hazard
   
Posts: 3440
Registered: 15-10-2015
Member Is Offline
|
|
I've been doing some reading in NFPA 45. It gives specific requirements for laboratory fume hoods in fire codes that have been adopted pretty widely
in the U.S.. This is the 2004 edition, so some updates have probably been made since then, but it contains a few requirements that I found surprising:
1. A fume hood is supposed to be able to contain a 2L spill.
2. A fume hood is supposed to have a flow sensing device permanently installed.
3. Many box fans cannot be used for ventilating a fume hood. There is a requirement that the motor and controls be out of the usual flow of air unless
approved for use in a fume hood. This surprised me mainly because I've used box fans that were permanently installed in a professional environment for
ventilating corrosive and toxic gases before, but those box fans were clearly designed and manufactured for that purpose.
4. An automatic fire protection system is required for handling flammable liquids in your fume hood unless it is constructed of materials with a Class
I flame spread rating: http://sfm.dps.louisiana.gov/doc_flamespread.html So it looks like drywall and fire retardant plywood are ok, but most plywood is not sufficient.
5. Flammable duct materials are not to be used except with "special local exhaust systems." I am planning on using aluminum, but it is interesting
that there is an exception for flammable duct materials.
6. The [optional] sash shall be "glazed" with materials designed to protect the fume hood's operator.
I'm planning on coating the inside of mine with gypsum, and my fan has a disc covering the motor and keeping it out of the flow of air, so I think it
be permitted to handle flammable liquids and just barely avoid the requirement of an automatic suppression system, although I will consider another
fan....
I'm not really sure what to think about the requirement that the sash be glazed. No specific glazing requirements are given, but a reference is made
to Annex C, an optional part of the standard on explosion protection. I think I will be ok with a rollup vinyl sash?
The part I'm not sure about is the permanent flow sensing device. Does anyone know what form that should take? Also, does anyone have a more
up-to-date version of NFPA 45?
Attachment: NFPA 45 2004 (1).pdf (3.2MB) This file has been downloaded 2366 times
[Edited on 22-7-2017 by JJay]
|
|
Geocachmaster
Hazard to Others
 
Posts: 146
Registered: 5-3-2016
Location: Maine, USA
Member Is Offline
Mood: Corroded, just like my spatulas
|
|
We got the main part of the hood built today and installed the blower in the window. Tomorrow we will install lights, sash, water and power, and we
will hook up the duct work.
As for the fan on amazon zts, I would say it's okay for fume hood. Not ideal though. The motor is partway in the path of the air. It also has air
intake of the opposite side of the flange. I will have to cover over this with tape. There are holes in the motor casing to allow air to pass through
and cool the motor. I'm not too worried about this though because the air current should keep corrosives out of the internals. This is for the 465 CFM
version so the 260 one might be different.
|
|
JJay
International Hazard
   
Posts: 3440
Registered: 15-10-2015
Member Is Offline
|
|
That looks quite sturdily constructed. Is that a baffle in the back?
I attached some vinyl to the front of mine with Velcro. I'm not 100% ready to recommend vinyl sashes for general use, but so far so good....
|
|
JJay
International Hazard
   
Posts: 3440
Registered: 15-10-2015
Member Is Offline
|
|
Oh and while researching glass glazing, I learned that "glazing" is simply the process of mounting a see-through panel. So a glazed sash is one that
contains a pane, and an unglazed sash would have an empty space. I guess probably everyone else knew that already, but it was new to me....
|
|
Geocachmaster
Hazard to Others
 
Posts: 146
Registered: 5-3-2016
Location: Maine, USA
Member Is Offline
Mood: Corroded, just like my spatulas
|
|
It is sturdy indeed. When it's finished I estimate the total cost to be $200, including the fan. If my dad charged me for labor then the cost would be
more like $800, but luckily he's working for free this weekend . There is in fact
a baffle in the back. 7 inch gap at the bottom, 1 1/2 inch gap at the top. I don't know what the best configuration is but I figured that most of the
air should be drawn over the work surface and some air out the top to get rid of less dense gasses. This baffle configuration just looked right to me.
|
|
JJay
International Hazard
   
Posts: 3440
Registered: 15-10-2015
Member Is Offline
|
|
I think the baffle was an excellent idea.
|
|
Magpie
lab constructor
   
Posts: 5939
Registered: 1-11-2003
Location: USA
Member Is Offline
Mood: Chemistry: the subtle science.
|
|
nice work, both of you
The single most important condition for a successful synthesis is good mixing - Nicodem
|
|
macckone
International Hazard
   
Posts: 2159
Registered: 1-3-2013
Location: Over a mile high
Member Is Offline
Mood: Electrical
|
|
Useful book if you don't want to buy a fan:
http://gingerybookstore.com/product36.html
This is relatively expensive for what it provides but could
be useful for someone that can't find exactly the right fan.
There are various baffles that can be used to keep a bunsen
burner from getting blown out by the air flow.
The simplest one is simply a U shaped piece of
sheet metal that is oriented away from the face.
|
|
macckone
International Hazard
   
Posts: 2159
Registered: 1-3-2013
Location: Over a mile high
Member Is Offline
Mood: Electrical
|
|
Also someone asked about air flow indicators.
The simplest air flow indicator is simply a ribbon
located near the sash opening. I have seen
these in labs to meet the NFPA requirement.
The other option is a pitot tube. The book I
mentioned contains instructions for constructing one.
|
|
JJay
International Hazard
   
Posts: 3440
Registered: 15-10-2015
Member Is Offline
|
|
I checked my local laws, and there's no specific NFPA requirement that I have to meet, but there is an IFC 2015 requirement:
5003.8.5 Exhausted enclosures. Where an exhausted
enclosure is used to increase maximum allowable quantity
per control area or where the location of hazardous materials
in exhausted enclosures is provided to comply with
the provisions of Chapter 60, the exhausted enclosure shall
be in accordance with Sections 5003.8.5.1 through
5003.8.5.3.
5003.8.5.1 Construction. Exhausted enclosures shall
be of noncombustible construction.
5003.8.5.2 Ventilation. Exhausted enclosures shall be
provided with an exhaust ventilation system. The ventilation
system for exhausted enclosures shall be
designed to operate at a negative pressure in relation to
the surrounding area. Ventilation systems used for
highly toxic and toxic gases shall also comply with
Items 1, 2 and 3 of Section 6004.1.2. The ventilation
system shall be installed in accordance with the International
Mechanical Code.
5003.8.5.3 Fire-extinguishing system. Exhausted
enclosures where flammable materials are used shall be
protected by an approved automatic fire-extinguishing
system in accordance with Chapter 9.
Chapter 9 mainly discusses sprinklers but also has reference to "alternative" automatic fire suppression systems and prescribes specific NFPA
sections.
|
|
Geocachmaster
Hazard to Others
 
Posts: 146
Registered: 5-3-2016
Location: Maine, USA
Member Is Offline
Mood: Corroded, just like my spatulas
|
|
I finished the fume hood on Monday night. I can't take good pictures, but I can take good video!
https://youtu.be/wijigT7xVIk
I'm very happy with it and it got its first use tonight. I did some smoke tests and everything looks good so far but I'm going to do something with
chlorine next week which will really test the fume hood.
|
|
JJay
International Hazard
   
Posts: 3440
Registered: 15-10-2015
Member Is Offline
|
|
Very cool. Mine needs some sort of baffle to ensure that both lighter than air and heavier than air gases are eliminated.
|
|
Reboot
Hazard to Others
 
Posts: 141
Registered: 8-8-2017
Member Is Offline
Mood: No Mood
|
|
I've started work on what I hope will be a small ductless hood eventually. I started with a nice heavy-duty professional kitchen table with a 12
gauge 304 stainless top. Stainless comes in a lot of grades; for a lab counter (or kitchen counter) you want either 304 or 316 (surgical stainless.)
Most other grades (like 430) aren't suitable; they corrode too easily from chemical exposure. 304 and 316 stainless is non-magnetic; you can't
stick a magnet to it. Cheaper grades are magnetic, so that's the easy test if you're wondering what something is.
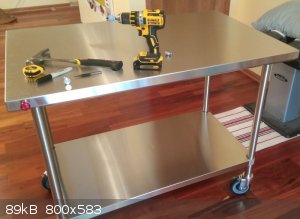
I'll be installing a number of panel-mount switches and gauges, which can give a very professional custom look with surprisingly little effort.
To start, carefully decide where you want the control to be and mark the center of the location.
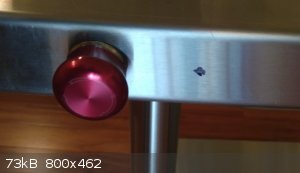
Next, take a narrow ('centering') punch and put it on the mark. Give it a good whack or two with a hammer, just enough to put a small indentation in
the metal. This keeps the drill bit from wandering off in the next step.
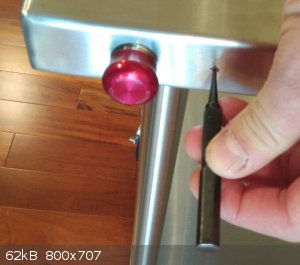
Chuck a hole saw into a decent drill (corded or more powerful cordless ones will work well.) The switch I want to install fits a 19 mm (3/4") hole,
so I'm using a 3/4" hole saw. The drill bit in the center of it guides the hole saw itself; start drilling with this bit in the indentation you made
with the punch. This is an easy process; just take your time and keep it strait.
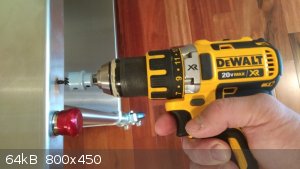
Once the hole is cut, the panel mount switch slides in from the front and a nut gets tightened onto it from the back to hold it in place. (This
switch is waterproof and has an o-ring on it to seal it to the panel. It can also light up when on, if you wire it that way.)
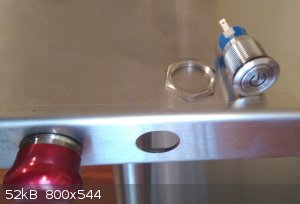
The wiring is a subject for another day. The system will use 12 volt DC for the switches (for both safety and due to power limits on these
switches.) The switches in turn will run relays that turn 120 volt AC power on and off to a number of items (hood fan, vacuum pump, coolant pump.)
The (already installed) red knob is an emergency kill switch; whack it and it will kill power to the whole apparatus. You can find these for about
$10. If you want something more glamorous/capable, Eaton makes a super-sexy $200 version. :-)
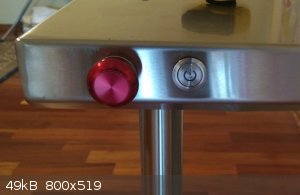
The plan is to eventually also install a vacuum regulator and some panel-mount vacuum/pressure gauges into the top of the table to one side. The
process for a gauge is similar, you just need a much bigger hole saw. I'd like to have at least one hood suction gauge (to verify good airflow) and
a big old 4" analog vacuum gauge at the least. The fan and filter system will be under the table (with some sort of enclosure for appearances)
There are still a lot of interesting design decisions to make before this comes together, but I'm having fun!
|
|
aga
Forum Drunkard
   
Posts: 7030
Registered: 25-3-2014
Member Is Offline
|
|
Today i found a small-ish industrial extractor at the scrap yard - 3.50 euros.
It verks !
Now to build a box so it can replace my feeble 'hood extractor.
Maybe then i'll have the guts to use that fume hood again in anger.
It's not been used much since i ended up inhaling a few lung-fulls of dioxane.
|
|
zed
International Hazard
   
Posts: 2277
Registered: 6-9-2008
Location: Great State of Jefferson, City of Portland
Member Is Offline
Mood: Semi-repentant Sith Lord
|
|
Whenever possible, I've worked my chemistry in a hood.
That being said, the high-tech, state of the art, hood that I mostly worked under, in college... Failed very reliably, whenever someone happened to
open one of the doors from the outside courtyard, into the lab. Especially so, on breezy or windy days.
Kind of like a fireplace, it would abruptly lose its "draw". In fact, despite perfect design, and a powerful fan, my fancy hood, would generally
blow "backwards".
The only remedy was to keep sharp ears, schedule experiments for quiet times, and when the outer doors were unexpectedly opened, to quickly lower the
glass and close the hood.
|
|
Texium
Administrator
      
Posts: 4516
Registered: 11-1-2014
Location: Salt Lake City
Member Is Offline
Mood: PhD candidate!
|
|
My fume hood blows out the rear wall of my garage, so I simply open the garage door about 6 inches to allow airflow to enter the room from the
opposite side.
|
|
Corrosive Joeseph
National Hazard
  
Posts: 915
Registered: 17-5-2015
Location: The Other Place
Member Is Offline
Mood: Cyclic
|
|
'How to Design Centrifugal Fans for the Home Shop' - David J. Gingery
"Build Inexpensive Powerful Blowers For Many Uses. . .
Build a dust precipitating cyclone, design sheet metal transition pieces, balance a dust collection system, build a static balancing stand and more.
Learn how to build a simple manometer and pitot tube and actually measure and fine tune your custom air system.
This book will show you how to take pillow blocks, shafting, plywood, sheet metal and other common materials and build a dirt cheap blower that
outperforms any make-do blower you might fine on the surplus market.
Let Dave show you how easy it can be to design a fan that will provide the volume and pressure you need for the system you're building."
http://libgen.io/book/index.php?md5=68E57ED8AEBDACEA7B372C4C...
/CJ
Being well adjusted to a sick society is no measure of one's mental health
|
|
MJ101
Hazard to Self

Posts: 82
Registered: 14-6-2018
Member Is Offline
Mood: Always Sunny
|
|
#macckone: Yes. A pitot tube is what you'd use, but there are also electronic devices.
https://www.epluse.com/en/products/air-velocity-instrumentat...
And of course, DIY. 
https://forums.ni.com/t5/LabVIEW-Interface-for-Arduino/Measu...
Of course you'll have to vett the sensor housing to make sure it will survive in the widest range of reaction.
|
|
Abromination
Hazard to Others
 
Posts: 432
Registered: 10-7-2018
Location: Alaska
Member Is Offline
Mood: 1,4 tar
|
|
Well I built my own for under 30 bucks from a plastic bin, a PC fan and some vinyl laundry duct. Not ideal for really dangerous fumes although its
great for everything else. If you have a budget and really need a good one, by all means follow magpie but this works well for small projects. I
uploaded it to instructables and will attach the link.
https://www.instructables.com/id/Fume-Hood-for-Under-30/
List of materials made by ScienceMadness.org users:
https://docs.google.com/spreadsheets/d/1nmJ8uq-h4IkXPxD5svnT...
--------------------------------
Elements Collected: H, Li, B, C, N, O, Mg, Al, Si, P, S, Fe, Ni, Cu, Zn, Ag, I, Au, Pb, Bi, Am
Last Acquired: B
Next: Na
--------------
|
|
CouchHatter
Hazard to Others
 
Posts: 146
Registered: 28-10-2017
Location: yes
Member Is Offline
|
|
Does anyone have any experience with or knowledge of air foils? I've searched the forum and there's very little talk of them apart from airplane ones.
They can reduce air rolls and turbulence in the hood, it seems like a good feature. Anyone have one on their hood?
The best documentation I've found is this file someone posted previously here. Not sure what book it's from, but I'd love to read the whole thing.
My hood design is a bit atypical and would struggle to integrate the air foil as is shown in the book. Maybe I need to redesign it.
|
|
Corrosive Joeseph
National Hazard
  
Posts: 915
Registered: 17-5-2015
Location: The Other Place
Member Is Offline
Mood: Cyclic
|
|
Laboratory Fume Hoods: A User's Manual
By G. Thomas Saunders
/CJ
[EDIT] - https://www.wiley.com/en-us/Laboratory+Fume+Hoods%3A+A+User%...
[Edited on 31-12-2018 by Corrosive Joeseph]
Being well adjusted to a sick society is no measure of one's mental health
|
|
CouchHatter
Hazard to Others
 
Posts: 146
Registered: 28-10-2017
Location: yes
Member Is Offline
|
|
You are like Beetlejuice, CJ. Thank you very much! I've got a copy on the way.
I'll be posting some photos soon too!
|
|
raffike
Harmless
Posts: 3
Registered: 24-6-2019
Member Is Offline
|
|
My simple hood. 150mm tube and almost 200 watt ventilator(not seen in picture. Stainless steel seems to handle everything just fine and pipe is
plastic. Have been in use for years and you can see,steel is like it just came from shop.
|
|
Pages:
1
2
3
4
5 |