Pages:
1
2
3 |
quicksilver
International Hazard
   
Posts: 1820
Registered: 7-9-2005
Location: Inches from the keyboard....
Member Is Offline
Mood: ~-=SWINGS=-~
|
|
Most possibly. However for an author like Spoonburger to write a "mia culpa" of that nature is quite something. He has contributed to a great deal of
energetic / pyrotechnic oriented material in organized and printed sources for many years.
The thing that strikes me is his recollection of pain which in an odd sense is a good thing as serious 3rd degree burns generally kill those nerves. I
also have milled Mg, however I had always be quite careful of the milling media & to always make damn sure the device(s) were grounded.
Again, from my experience, Mg mills finer and finer in a granulated form; not crushing into flakes or similar shapes. In fact I have seen Mg SO fine
as to be difficult to ignite if not separated quite a bit; almost forming a solid in it's fine particulate form.
It's likely that Loyde got it right on the money. That the dry silica formed a static phenomenon with the movement of the mill and that was all that
was needed.
Once, quite some many years back there was an aluminum that was available for a short time that had a coating of Teflon! This was some of the most
reactive aluminum I had ever seen; perhaps the most. As the story goes it was pulled from some floor sweepings of an aerospace industry plant &
was milled once in a large quantity with both lead and Lignum Vitae (Iron Wood) croquet balls in a cement mixer. Perhaps the reason it did not cause a
disaster is the combination of media and lack of air seal.
It most certainly DID have it's hand in many problems during it's sale to the public.
Included below is an interesting patent that uses either terephthalic acid (the better result) or pentaerythritol (less effective) to create a flash
powder that claims not to be explosive without containment but with containment is an extremely powerful explosive mix. This (if true) would add a
HIGH element of safety to both burst charges or simulators - virtually any area where an extremely loud explosion is needed but safety is primary.
Attachment: _6521064-flash.pdf (44kB) This file has been downloaded 838 times
[Edited on 29-11-2010 by quicksilver]
|
|
nitro-genes
International Hazard
   
Posts: 1048
Registered: 5-4-2005
Member Is Offline
|
|
Very interesting, I was sceptical at first, having seen only peak pressures mentioned in the patent, but total impulse also seems twice as high as
with regular FP.
Unconfined, the 72.9/18.5/8.6 composition is nearly impossible to light, even with a gasburner. Loosly packed in sealed cardboard tube and lighted by
fuse it burns slowly (though very steady!) with yellowish/white flame. The cardboard tube (quick test) probably didn't provide enough pressure to make
DDT. That is the only serious drawback I can see, maybe intermediate PE contents/higher Al could be used to overcome this high pressure thresshold for
this comp. to work. Another thing would be using chlorate instead of perchlorate or adding a catalyst like Fe2O3. Haven't tessted this yet, though the
comp. with perchlorate seems amazingly inert.
So whats the deal here? IIRC they mentioned sublimation of the PE? Would other polyols qualify as well? Erythritol, sorbitol, etc?
|
|
The WiZard is In
International Hazard
   
Posts: 1617
Registered: 3-4-2010
Member Is Offline
Mood: No Mood
|
|
Quote: Originally posted by quicksilver  |
Included below is an interesting patent that uses either terephthalic acid (the better result) or pentaerythritol (less effective) to create a flash
powder that claims not to be explosive without containment but with containment is an extremely powerful explosive mix. This (if true) would add a
HIGH element of safety to both burst charges or simulators - virtually any area where an extremely loud explosion is needed but safety is primary.
|
Flash compositions of some types will cause explosions in the
lightest of containers even sometimes in just a few turns of paper
but it also happens that these compositions are extremely brisant
and sensitive. Horrifying mixtures of potassium chlorate, pyro
aluminium, sulphur and barium nitrate have been employed and
should be avoided at all costs. Mixtures of the perchlorate, sulphur
and bright aluminium are safer and appear to be used extensively
in the U.S.A. and Japan, but even these would be considered
dangerous by many of us in Europe. In fact the more common
European technique is to use a strong paper tube with a
composition consisting simply of potassium perchlorate and dark
pyro aluminium.
Rev. [The Master Blaster Pastor]
Ronald Lancaster Fireworks: Principles and Practice
djh
----
Pyrotechnics don't have
to be a dying art. /djh/
|
|
nitro-genes
International Hazard
   
Posts: 1048
Registered: 5-4-2005
Member Is Offline
|
|
Even 70/30 KClO4+DG Al by itself is pretty sensitive, both to static discharge and friction. Put a few mg's in a mortar and see how easy it flashes
from the resulting friction. The PE addition somehow makes the composition nearly completely inert when unconfined, the difference is really quit
dramatic and not even remotely comparable with "regular" flash. I was suprised to see the steady burn rate of this composition at all.
|
|
quicksilver
International Hazard
   
Posts: 1820
Registered: 7-9-2005
Location: Inches from the keyboard....
Member Is Offline
Mood: ~-=SWINGS=-~
|
|
I had thought the patent interesting as I had not seen something of this nature before with such emphasis as to gain a full patent. The selection of
terephthalic acid to a 70/30 is what interests me most as there may be factors such as the gaseous by product of (terephthalic acid) making for
ignition perhaps even enhancing it; but in it's solid state being a retardant to combustion.
Obviously the need for understanding what happens to terephthalic acid during a burning process would determine why (or if) this patent fills it's
promises.
Personally I would not waste reagent-grade pentaerythritol on something like this but the garbage in drums that is often sold (in the vinyl paint and
coating businesses) is a different story. However in today's climate of fear and stupidity I would not attempt to buy a can any longer. Terephthalic
acid unfortunately is not available in a low technical grade (TTBoMK) but I don't think it's too pricey.
[Edited on 1-12-2010 by quicksilver]
|
|
Mumbles
Hazard to Others
 
Posts: 436
Registered: 12-3-2003
Location: US
Member Is Offline
Mood: Procrastinating
|
|
Quote: Originally posted by mnick12  | I have heard of incidents similar to this, some causing quite a bit of damage. A particular incident I recall reading a few years back was an
experienced pyrotechnic hobbyist, who wanting some ultra fine magnesium, milled some coarser granules to get the desired particle size. Upon opening
the ball mill the magnesium dust instantly ignited causing a massive fireball with alot of heat, miraculously the man escaped with only mild burns.
|
When I read that I thought of another accident actually than Lloyds. It happened to Bob Forward, but I am not sure if it was Mg or MgAl, but I lean
toward magnesium. The accident actually didn't happen when he opened the mill, but rather when he was dropping or pouring the dirty media back into
the uncleaned jar.
Lloyd is a person well versed and well respected in pyrotechnics, so I will let his story be. I do have a bit of an issue believing the jar was still
intact. I had a pretty major accident recently with much cooler burning materials, and PVC a fair distance away was melted very severely.
With regard to milling of aluminum both stearic acid and oleic acid are fairly common with nearly every type of flake aluminum, even the blackheads
and dark aluminums. I've seen the aluminum carbide theory mentioned before, but have never heard anything that would convince me one way or the other
if it is just carbon/stearic acid, an aluminum carbide protective surface with a highly scattering surface, or a combination of both that gives the
dark color and protection. There is certainly some fatty acids in there though. I've also heard some people claim the aluminum carbide improves
reactivity. A drum of Eckart #5413-H reads the following though:
Aluminum >/= 90%
Aluminum Oxide < / = 4%
Stearic Acid < / = 2%
Carbon < / = 2%
I'm curious as to why you'd try using lead to mill aluminum. Even hardened lead is softer than aluminum. I'd imagine this would result in fairly
significant lead contamination of the aluminum powder. Most who try to make their own flake aluminum, or reduce the size of MgAl, use steel. Again,
I'd leave the glass marbles out. It's pretty clear you're trying to use this to make flash, and abrasive materials are not something I would want to
be adding.
|
|
nitro-genes
International Hazard
   
Posts: 1048
Registered: 5-4-2005
Member Is Offline
|
|
I go with the increased reactivity of the aluminium carbide coating, it seems that even with nanopowders like ALEX, a coating of palmitic acid is
enough to prevent further oxidation of the aluminum upon storage.
Interesting stuff these nanopowders, I've been thinking about a way to produce them OTC for a long time. Commercially they are made by explosive
evaporation in inert surrounding gas, particle sizes go as low as 100 nm. Lots of potential in pyrotechnics, HE and rocketry...
--> http://www.nanosized-powders.com/en/35/
|
|
Mumbles
Hazard to Others
 
Posts: 436
Registered: 12-3-2003
Location: US
Member Is Offline
Mood: Procrastinating
|
|
The reason I've always been suspicious of the aluminum carbide theory is that every intentional preparation of it utilizes far higher temperatures
than would be experienced if just charring the paper off. You'd also think you'd be able to see yellow crystals on the surface. Not to mention it
decomposes with moisture, so I would imagine any aluminum carbide that may would be decomposed within at most a few months of it's production.
|
|
quicksilver
International Hazard
   
Posts: 1820
Registered: 7-9-2005
Location: Inches from the keyboard....
Member Is Offline
Mood: ~-=SWINGS=-~
|
|
I also can attest to the problem w/ using lead as a medium. I stopped after a single day. However the result will yield some substantial reduction at
that point but the contamination is something that occurs no matter the material if metallic. However, in hindsight, I am not sure the level may be as
great as it may initially seem as the surface of the lead become coated with Al particulate & the crushing / shaving effect may be more than
direct contact. But I always want to opt for purity so I dismissed it.
Even brass had some contamination and the problem of introducing copper elements into anything that may contact a perchlorate/chlorate is a serious
one. Glass appears to be a fairly decent material but finding anything but large marbles is tough. Personally I don't mill unless I am going to be
doing a fairly substantial amount as I have the setup for it and it just seems a waste to mill much less than a pound
I also think that the "open" or free volume in a mill can contribute to problems as well as a more full mill may utilize the "shaving effect" to an
advantage.
There is a factor that is often unconsidered; & that is that direct contact of medium and milled material is often much. much less than most
people think. The shaving or crushing effect is often what takes place and for that, the medium needs weight. Even glass is quite light unless the
volume is fairly large.
The preparation is (IMO) one of the significant agendas of working this effectively. The "water and cut foil" prep in a blender had been the better of
many as it has an element of safety and size reduction is fairly good if a blender used is one that could stand up to long runs. If that is not
available; the user needs to be satisfied with a much lessened rending of the foil.
The best starting material I had found was floor sweeping due to that "shaving factor" so as to produce a granular mater prior to further rending
& flattening. The problem of cleaning up from contamination of dirt and debris is one that is very tough to avoid but (IMO) worth the effort as
you generally have several pounds to work with at minimum. I had once totally forgotten to place the milling medium in the mill when I was first
beginning to ball mill materials and found that the simple act of tumbling the floor sweepings had a great result. Therefore it's just my opinion that
with Al (and perhaps Mg) the actual SAME material is the best milling media one can use! Several large cubes (or best; spheres) of Al may actually be
the best if time is not a factor. The problem occurs when the mill uses a volume area that doesn't allow for a distance fall. A 6" diameter doesn't
allow a "dropping" of the media and milled element to take place to gain a crushing effect.
There is a remarkably thin (viscosity) oil available which is a synthetic used for pump lubricant that is really the only thing I have used in the
past. A tiny bit goes a long way. In it's refined state it's used as microscope oil due to it's remarkably thin viscosity (it only had a "mil-spec
number" as I remember but it is common as a pump oil referred to as "ultra fine". 2-3ml per lb of Al is MORE than enough & once the mill has been
turning for a few days the majority will adhere to the walls and be left behind from the product.
The draining of the water from the initial blender rending will allow enough oxide to develop prior to milling. And in the case of floor sweepings,
there should be enough oxide there after a day of more air exposure.
It occurred to me that Loyde must have known that a true "outside ground" of the whole unit is a demand that has to be met. A third prong ground of
the motor just doesn't cut it. The whole unit needs a real full ground of "rod in earth" type. I think he even had written that!
There had been some discussion of using a conductive container in a mill (paint can) rather than rubber, etc as it could be grounded more effectively.
I have never tried that as an experiment I was not willing to risk the consequences.
[Edited on 2-12-2010 by quicksilver]
|
|
The WiZard is In
International Hazard
   
Posts: 1617
Registered: 3-4-2010
Member Is Offline
Mood: No Mood
|
|
Quote: Originally posted by quicksilver  | I also can attest to the problem w/ using lead as a medium. I stopped after a single day. However the result will yield some substantial reduction at
that point but the contamination is something that occurs no matter the material if metallic. However, in hindsight, I am not sure the level may be as
great as it may initially seem as the surface of the lead become coated with Al particulate & the crushing / shaving effect may be more than
direct contact. But I always want to opt for purity so I dismissed it. |
I would note in passing commercial producers of milled aluminium
anneal it before milling w/ steel balls. Aluminum is tooo soft as manufactured.
At no extra charge —
GOLD-BEATERS SKIN. This skin is prepared from the external or peritoneal
coat of the cæcum or blind gut of neat cattle. [Neat cattle — from whom is obtained “neat’s foot
oil”. /djh/] The workman separates and turns over the portion which encircles the
junction of this pouch with the rest of the intestines, and draws it off inverted form
the other coats to the length of 25 or 30 inches. It is then immersed a short time
in a weak solution of potash, and is cleaned by straying upon a board with a
knife. When thus well cleaned and by soaking in water, the piece is stretched
upon a kind of frame from 40 to 50 inches in length and 11 inches wide, and
made up of two uprights held together by two cross-pieces having longitudinal
groves two and a half line in width. The surface of the membrane which was
outside in the animal, is placed in contact with the upper part of the frame ; it is
stretched in every direction, and is glued to its rim. Another membrane is then
stretched above the first, with its external surfaced placed upwards, and is
attached to it by glueing around the edges. When dry, the membranes are
separated by running a sharp knife along the groves. Each strip is then glued up
a frame similar to the first one, but without a grove, and is washed over with a
solution composed of alum 1 ounce ; water, 2 quarts.
When the surface is dried, a sponge dipped in a concentrated solution of fish-
glue in white wine, rendered aromatic by cloves, nutmegs, or camphor, is passed
over it. When this coating is dried, it is covered with a coat of white of eggs, and
the strip is cut into pieces 5 ½ inches square, which are then smoothed out under
a press, and make up into leaves.
A body is given to the pieces of gut ; that is, they are moistened with an infusion
of cinnamon, nutmeg, or other warm and aromatic ingredients, in order to
preserve them ; an operation repeated after they have been dried in the air .
When the leaves of the skin are dry, they are put into a press, and are ready for
use. After the parchment, velum, and gut-membrane have been a good deal
hammered, they become unfit for work, till they are restored to proper flexibility,
by being placed leaf by leaf, between leaves of white paper, moistened
sometimes with vinegar, at others with white wine. They are left in this condition
for three or four hours, under compression of a plank loaded with weights. When
they have imbibed the proper humidity, they are put between leaves of
parchment 12 inches square, and beat in that situation for a whole day. The are
then rubbed over with fine calcined gypsum, as the vellum was originally. The
gut-skin is apt to contract damp in standing and therefore dried before being
used.
GOLD-BEATING……. 2 pages.
Ure’s Dictionary of Arts, Manufactures, and Mines: Containing A Clear
Exposition of their Principles and Practices.
By Robert Hunt, F.R.S.
Longman’s, Green, and Co. 1878
Volume 2, p. 727-728.100
|
|
The WiZard is In
International Hazard
   
Posts: 1617
Registered: 3-4-2010
Member Is Offline
Mood: No Mood
|
|
Ball milling aluminium
Found this in the depths of my HD.
Aluminum Powders and Pastes
“The Tale of The Powdered Pig”
Reynolds Metal Company 1960
DEVELOPMENT OF ALUMINUM POWDERS
Use of thin metal foil or "leaf" for decoration and ornamentation dates back to early
Egyptian days when the art of overlaying wood, bone and other materials with gold or
bronze was developed. Through the ages this art spread over China, India and later
over Europe. Its height perhaps was reached in the fabulous extravagance of Louis the
14th in whose court the glitter of gold leaf reached world renown.
Gold particles were melted, cast into bars, hammered down into thin sheets. These
were reduced still further in thickness by interleaving with goldbeaters' skins and
pounding the pack with a heavy hammer, producing leaf only a few millionths of an inch
in thickness. In beating to thin leaf, certain particles broke off at the edges of the leaf.
The artisan soon found, however, that these particles could be stuck together with egg
white or other materials to look like a continuous leaf. Next step was to use such
particles to form a paint for ornamenting chinaware, porcelain enameled objects and
similar work.
Then leaf scraps were shredded by rubbing through a fine mesh screen to form a
powder that could be utilized in paints. However, such powder was expensive, so
similar powders were made from copper and bronze. Eventually base metal alloys
colored by heat treating, were developed to duplicate almost every tint of the rainbow.
"Silver bronze" powder was made either from tin or silver. Making powder from tin
involved certain difficulties, while silver was expensive.
Thus the advent of aluminum powder about 1890 resulted in rapid adoption by the
bronze powder industry. This pigment was called "aluminum bronze" even though not
made from a bronze alloy. Modern "aluminum bronze" pigments are made from high
purity aluminum.
Thus this reference to "bronze" has been carried down into today's usage by the metal
powder industry and is sometimes confusing to metallurgists not familiar with this
historical background.
Early Production Methods: Possibly the first metal powder was made by hammering
scraps of gold leaf or grinding in a mortar and pestle. Rubbing scraps of gold leaf
through a fine mesh wire sieve perhaps was next employed. These tedious manual
methods of the goldbeater, however, were replaced by mechanical methods around
the middle of the 19th century to give birth to the modern bronze powder art.
Today mechanical stamps or ball mills reduce the aluminum feed to powder by many
light blows. Ball mills are huge cylinders carrying a charge of aluminum powder and
steel balls. As the cylinder is revolved, the balls are caused to cascade down against
the inner wall, reducing the aluminum particles to flake powder by the multiple impacts
so produced.
Aluminum powder is also made by atomizing molten aluminum, allowing the molten
spray to harden in a blast of air.
Early Applications: Until the latter part of the 19th century, the cost of metal powders
limited their use largely to decoration and ornamentation of jewelry, chinaware,
porcelain enameled work and objects d'art.
With the development of the bronze powder industry and greatly reduced cost of the
powders, application expanded greatly.
A very fine powder was developed for striping or "lining" coaches and other vehicles.
The term "lining", referring to fine powders, is a carryover from this period.
However, "fine" powders of the older days were only 120-140 mesh. Now it is possible
to produce powders so fine that 99.99% of a sample will go through a 400-mesh screen
(although all official reports are based on quantity through a 325-mesh screen as this is
the finest screen certified by the U. S. Bureau of Standards).
The finest powders are usually furnished in paste form, (mixed with sufficient liquid to
form a paste), since the extra fine powders are easier to handle and use in this form.
Types of Powders: Aluminum powders can be divided into two broad classifications —
flake and granulated. The length or width of a flake particle may be several hundred
times its thickness; whereas the length, width and thickness of a granulated particle are
all of approximately the same order, the length dimension probably not exceeding two
or three times the thickness dimension. Flake particles are thus essentially flat, while
granulated are more or less spherical or sausage shaped. The different characteristics
and applications of the two types will be explained later in sections under those
headings.
MODERN PRODUCTION METHODS
First advance in production methods came with the substitution of mechanical means
for the laborious handwork of the goldbeater. Sir Henry Bessemer was so intrigued by
the possibility of making a profit of nearly $25 per pound by converting brass to "gold"
bronze powder that, after concentrating on the problem for several years, he finally
developed a satisfactory mechanical production method and profited greatly there from.
In fact, he dominated the market for many years.
While the problem of producing fine particles of metal mechanically is not difficult, it is
not so easy to give them the shape, brilliance and other characteristics required. As is
explained more fully under characteristics, page 62, the powder particles must be flat,
have smooth surfaces, be separated from each other and have surface characteristics
that permit one particle to slide over another easily (flow). Also the color must be right.
All these characteristics require certain things of the production methods. The best
quality powder appears to be that produced by a large number of light hammer blows,
affording the metal an opportunity to spread out, break off, work harden, etc. as will be
explained.
Today, three different methods of producing aluminum powders are in use at the
Louisville plant of the Reynolds Metals Company — the largest plant of its type in the
world. Flake powders for chemicals and explosives are produced dry by stamping or
hammering extremely thin aluminum foil. Pigment powders are produced as a paste by
ball milling granular powders in a liquid, and subsequent drying. Granular powder is
produced by atomizing molten aluminum. Each method produces a powder with
individual characteristics, so each method will be described in detail for a better
understanding of how to use the resulting product.
In addition to these, there are other methods of producing aluminum in finely divided
form. "Grained" aluminum consisting of rough irregular particles 1/64 to 1-inch in length
results when molten aluminum is stirred while it is solidifying. "Granulated aluminum" in
the form of flattened drops up to 1/2-inch in diameter are made by pouring molten
aluminum through a sieve into water. Shot is made in the same manner. The small
particles resulting from grinding and sawing operations also have certain uses.
Atomizing: In general granular powder produced at Reynolds is made by atomization.
Pig aluminum is melted in a furnace. As the molten aluminum flows through a small
orifice in the atomizing head, it strikes a stream of air. This breaks up the liquid
aluminum into many small particles to form a spray which is directed into a receiver.
There it solidifies or freezes to form fine particles, roughly teardrop or spherical in
shape. These particles then are blown on through the duct to a structure housing a
series of canvas bags for collecting the granular aluminum powder.
Stamping: Whereas production of powder by atomizing is a fairly simple process
involving essentially a single operation, producing the flake powder by stamping
requires a number of operations. Particle size in atomizing is controlled by air and metal
temperatures and by spray nozzle adjustment. In stamping, many more factors enter
the picture.
Thickness of original foil material; number, force and rapidity of the individual hammer
blows; number of hammering stages employed; type and amount of lubricant;
arrangement of air agitation and discharge; amount of polishing; etc. — all have an
influence. Also number and selection of screening operations between hammering
stages greatly affect the final product. It is these wide variations in the manufacturing
process that are employed in producing the many types of powder to provide exactly
the characteristics most suitable for each particular application, in the chemical or
explosive field. Reynolds powders stamped from foil are not supplied for pigment
purposes.
Raw material for stamped flake powder is largely in the form of foil from Reynolds foil
plants. The foil must be free from materials such as oil, grease, dirt, iron or other
substances. Also no aluminum alloys can be tolerated because they do not reduce
properly under the hammers, due to their high mechanical properties.
In order to remove the effect of work hardening during rolling and to make the material
as workable as possible, it is first cleaned and annealed; then cut up into particles small
enough to pass through a screen with ¾ -inch openings. Further reduction is by
hammering in stamping mills.
These stamping machines are of several different types. All have multiple hammers
raised by cams and allowed to fall to strike the steel anvil by force of gravity. Anvil and
lower end of hammers are enclosed to confine the powder. Additional material is fed
into the mill at frequent intervals while discharge is continuous. Material at this stage will
pass through a screen with 20 openings to the inch (20-mesh screen).
Lubricant is necessary to prevent the small particles from welding together under the
impacts from the hammers. Lubrication also facilitates spreading of the metal under
impact, thus increasing the rate at which large flakes are broken up into small flakes.
Stearic acid is commonly used, although tallow, olive oil, rape oil or other oils may be
employed.
Action of the hammers in beating out the metal into thinner and thinner flakes work
hardens or embrittles the material and so assists breakup. At the same time,
hammering one flake over the edge of another produces a shearing action that further
aids reduction of particle size.
Mills in the third stage usually employ more hammers, operate faster, produce a
greater number of lighter blows than the second group of machines. All mills are in
banks as shown in accompanying illustrations. These, like the other mills, are charged
at regular intervals (such as 1-hour) with the air discharge being continuous. Fourth and
fifth stages may be utilized for certain types of product, although particles from this third
stage will pass through 40 to 300-mesh screens, depending upon length of time in the
mill.
As will he further explained under characteristics, page 62, and under testing, page 66,
any particular powder rarely has all particles of the same size, unless specially made.
Most powders contain a certain amount of fines of a certain size range, with some
larger particles.
Grading: In any case, grading to size is an essential step in production. Grading is done
by screening through silk bolting cloth or wire sieves. A typical screen will be of 100-
mesh silk with a working area about 3 x 7 feet. As shown in accompanying illustration,
cloth spouts and covers are employed to prevent the fine powders from becoming
suspended in the air in the room. Material not passing through the screen is taken back
to the hammer mills and reworked. Various sequences of hammering and screening
may be employed. Tests for size, quality, etc. are made at every stage of manufacture.
See section on testing, page 66.
Polishing: For many applications where a brilliant characteristic is desired, the flakes
are actually polished by brushes in a drum. Illustration page 11 shows a typical polishing
room scene. Brushes usually revolve within the stationary drum.
Action during polishing is threefold. First a lubricant is applied to the surfaces of each
flake particle. Then the rubbing action develops heat which softens the lubricant or
polishing agent (usually stearic acid, a dry powder) and also helps distribute it over the
surface of the flake in extremely thin and uniform layers. Third, rubbing the flakes
between the brush tip and innerwall of the drum flattens and smooths out the flakes.
See further discussion under characteristics, page 62.
Wet Ball Milling: Most all aluminum pastes and some powders are made in ball mills.
High purity atomized aluminum powder is normally used as the raw material. It is
charged into a large cylindrical drum along with a lubricant, a suitable liquid and a
quantity of steel balls. The drum is placed with its axis in a horizontal position and
revolved. By adjusting speed of rotation, size and number of balls as well as amount of
aluminum charged into the drum, it is possible to produce an operating condition where
the balls "cascade" to provide a large number of hammer-like impacts as they fall
against the inner wall of the drum.
This action closely simulates the hammering in the stamping mills. This is desirable
since hammering produces a high quality powder characterized by a bright, glossy
surface that has the brilliance, luster and color desired. In ball milling, the lubricant is
used to avoid welding the particles together under impact. An inert liquid such as
mineral spirits is also added to form a carrier for the aluminum particles.
From the ball mills, the slurry goes through a filter to remove excess liquid. The filter
cake contains aluminum pigment with some mineral spirits. A metal content of 65-75
per cent gives a stable paste suitable for use in most coatings.
Driers may then be employed to reduce the spirit content still further or will completely
dry the mixture when dry powder is desired. Thus powder as well as paste can be
made in the ball mills.
The wide variety of powders and pastes described in this book are thus made by
various methods, different hammering sequences, types of lubricants, screening
sequences, etc. It thus becomes evident that making a high grade aluminum powder or
paste with characteristics precisely adjusted to the requirements of any particular
service is a task demanding the highest technical skill, long experience and ultra-
modern equipment.
|
|
The WiZard is In
International Hazard
   
Posts: 1617
Registered: 3-4-2010
Member Is Offline
Mood: No Mood
|
|
Ball milling book or two
I shelve — and you may find interesting.
A treatise on the internal mechanics of ball, tube, and rod mills
Horace Edgar Rose, Ralph Major Edward Sullivan
Constable, 1958 - 258 pages
(Not found @ google.com/books)
Amazon.com pop'd up these :—
High-Energy Ball Milling: Mechanochemical Processing of Nanopowders by M. Sopicka-Lizer (Hardcover - Jul 7, 2010)
Buy new: $239.95
Mechanical Alloying And Milling (Dekker Mechanical Engineering) by C. Suryanarayana (Hardcover - Sep 28, 2004)
Buy new: $219.95 $188.26
Excerpt - Table of Contents: "... 11 2.1. Introduction 2.2. Historical Background 2.3. Development of High-Energy Ball Milling 2. ..." Surprise me!
See a random page in this book.
Mathematics and Control Engineering of Grinding Technology: Ball Mill Grinding (Mathematics and its Applications) by L. Keviczky, M. Hilger, and J.
Kolostori (Hardcover - Mar 31, 1989)
Buy new: $239.00
Bet it's a real page turner! Not.
[Edited on 2-12-2010 by The WiZard is In]
|
|
franklyn
International Hazard
   
Posts: 3026
Registered: 30-5-2006
Location: Da Big Apple
Member Is Offline
Mood: No Mood
|
|
So the gist is - you can beat our prices , but you can't beat our balls ?
I think I'd rather have a lap dance to bump and grind aluminum.
.
|
|
watson.fawkes
International Hazard
   
Posts: 2793
Registered: 16-8-2008
Member Is Offline
Mood: No Mood
|
|
I think I'd prefer a crotch that wasn't on
fire.
|
|
The WiZard is In
International Hazard
   
Posts: 1617
Registered: 3-4-2010
Member Is Offline
Mood: No Mood
|
|
Quote: Originally posted by franklyn  | So the gist is - you can beat our prices , but you can't beat our balls ?
I think I'd rather have a lap dance to bump and grind aluminum.
. |
Ah a Big Apple residence — you must be thinking of the
Melody Theater long gone from W 48th Street.
Wiki-P Lap dance and follow the obvious links for more info.
|
|
The WiZard is In
International Hazard
   
Posts: 1617
Registered: 3-4-2010
Member Is Offline
Mood: No Mood
|
|
Ball Milling Speed and Load
Rose and Sullivan
Ullmann's B2 5th ed.
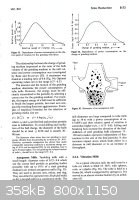
djh
-----
How I came to have volume A1-26
and B1-8 of the 5th ed of Ullmann's?
eBay. Found it at a price I could justify
and close enough that the shipping wasn't
a deal breaker. As with most of what I
buy on eBay I was the only bidder.
I inquired of the seller - where did you get
this brand new set? He was a commercial
photographer and the publisher sent him
the set for an ad. and didn't want it returned! A
complete set was ca. US $12 000!
After several years of effort I found the 27 & 28
volumes at a reasonable price.
For chemistry I prefer K & O. I own the 3 and 4th
ed. I have looked at the 5th or latter ed but prefer
the earlier eds. Someday I'll find the 1st ed for a
good price.
|
|
quicksilver
International Hazard
   
Posts: 1820
Registered: 7-9-2005
Location: Inches from the keyboard....
Member Is Offline
Mood: ~-=SWINGS=-~
|
|
-=OT blurb=-
Now the PRICES of texts on energetic materials and associated sciences is a whole topic in itself. I too, have attempted to put together a functional
collection of books over the years and at this moment I would say without exaggeration I have at least $2500-30000 in books I've bought (striving for
a decent deal at each turn) and working used book sales and library sell-offs.
Lap-dances: Hell, you could get a month of Happy Endings for the money it would take to get some of the more recent publications. And although I know
we have already discussed Albris and other used book sellers; I do have a method that MAY help one or two of you get some more textbooks at a decent
price.
Contact a "Librarian's Association" in a smaller community (they are general county-oriented groups of working-level librarians who join together to
attempt to pull more money for their own branches) and tell them you are looking to BUY books in specific categories in rough condition and that you
are a "continual source" to buy off these type of books. - YOU WILL GET CALLS BACK! They are hungry for money and they really don't see any value in
what (to many of us) would be a gold-mine of information. That's how I got most of the PATR. Usually the names are (County name) Librarian's
Association, or collective, or something damn similar & will take a bit of hunting but they may be listed or on-line.
|
|
franklyn
International Hazard
   
Posts: 3026
Registered: 30-5-2006
Location: Da Big Apple
Member Is Offline
Mood: No Mood
|
|
@ The WiZard is In
You are seriously afflicted with bibliophilia. No doubt
you haunt the stacks of the Strand on 11th street.
Regarding
" As with most of what I buy on eBay I was the only bidder. "
Ever lose out on an opportune find on Ebay ?
You might try sniping.
Gixen is a last moment bid entry service that's free.
I've had good results , the logon is not private but
no charges of unauthorized use have surfaced.
www.gixen.com
.
|
|
quicksilver
International Hazard
   
Posts: 1820
Registered: 7-9-2005
Location: Inches from the keyboard....
Member Is Offline
Mood: ~-=SWINGS=-~
|
|
He's not the only one; I caught it (bibliophilia) back in the UseNet days when a certain person used to post there quite often. But seriously; you
(Franklyn) have found some GREAT stuff online. I know because I still hunt and some of the links you've found have slipped right through my fingers...
:-)
|
|
Armistice19
Hazard to Self

Posts: 87
Registered: 19-6-2007
Member Is Offline
Mood: Brain sponge activated!
|
|
Recently I purchased three boxes of chrome plated steel milling media (50 balls each box). I also took the advice that all of you have so kindly
posted and bought 1lb of stearic acid as well. With these new products I will attempt the same synthesis and post the results. Thank you for all of
your assistance.
[Edited on 9-12-2010 by Armistice19]
“Imagination is more important than knowledge. For knowledge is limited to all we now know and understand, while imagination embraces the entire
world, and all there ever will be to know and understand.” -Albert Einstein
|
|
quicksilver
International Hazard
   
Posts: 1820
Registered: 7-9-2005
Location: Inches from the keyboard....
Member Is Offline
Mood: ~-=SWINGS=-~
|
|
Just as an aside Skylighter is selling a rock tumbler (a common ball mill design) for $79, which (if it is the same as the Harbor Freight unit made in
China - they appear the same.....) actual cost is $29.
Rock tumblers are attractive due to low cost, completed assembly and rubber containers. But they are tough to really ground properly & will always
be totally air-tight. These are not always seen as advantages.
Ball milling should be done out of doors, they should be grounded as well as possible (the whole unit: not just the motor or frame) & a tiny
amount of "breathing" is a positive thing; stopping large amounts of hydrogen or other gases from building. They should also be worked with remotely:
even if that simply means along extension cord. When stopped; they should be allowed to come to a "resting period" for a few moments. This settles the
crushed material and allows the ground to do it's job. dielectric and conductive elements can even produce a capacitive phenomenon to a slight degree
and a moment's resting is a safety issue that has some dividends.
|
|
gregxy
Hazard to Others
 
Posts: 421
Registered: 26-5-2006
Member Is Offline
Mood: No Mood
|
|
It would also be interesting to investigate if aluminium carbide is what makes the "dark german" powder better.
Perhaps someone could:
1. Grind Al foil in an air tight container for several days
2. Add powdered graphite, lampblack or charcoal without letting much air in.
3.Continue grinding.
4. Stop grinding and carefully introduce air.
Another alternative would be to grid with steric acid and then
roast the product without air to pyrolyze the organic coating.
|
|
Mumbles
Hazard to Others
 
Posts: 436
Registered: 12-3-2003
Location: US
Member Is Offline
Mood: Procrastinating
|
|
I really doubt that the mechanical grinding would impart enough energy to form aluminum carbide. You'd probably end up with nothing you couldn't get
from an unethical reseller of aluminum. I also have a feeling that trying to burn off a stearic acid coating would make quite a mess, as it would
fuse first before pyrolysing.
If you want to test this aluminum carbide theory, I'd imagine you'd perhaps want to wash the coating off of a powder, and try to roast the aluminum
powder with a little graphite using conditions known to generate aluminum carbide. You could then do some tests side by side with the decoated
powder, and the powder which has been roasted.
|
|
quicksilver
International Hazard
   
Posts: 1820
Registered: 7-9-2005
Location: Inches from the keyboard....
Member Is Offline
Mood: ~-=SWINGS=-~
|
|
The unethical agenda of "Indian Dark" (the most common one where they adulterate with carbon) was actually caught by about 4 or 5 people. I think I
may have been one of them.
I had bought some years back and it just felt odd. Putting in a microscope reveled that the carbon was not attached; the way it would have been from
the old fashioned burning foil-paper. & there was MUCH too much carbon. A fellow who I used to trade with contacted me and wanted to trade for
some straight rolled rocket tubes that I wanted. I didn't want him to get the idea that I was screwing him so I said what I believed. He got a sample
from me and said he had never seen anything like that before (it was sold by a large pyro supplier AND a very large specialty importer).
I took a tiny sample an used an oil lens at 1000x and it became very clear that the carbon was never attached and was an obvious (air float) wood
carbon. One guy continued to sell it off but the large supplier would not sell it and made a really big deal out of it with the importer. It's all
gone now as that was years back. It was way too obvious as it actually settled if you had the right equipment.
Getting back to carbide: I think it would be just too dangerous to work that in a ball mill. I think it may be possible to do on a very small scale in
a lab environment but I believe it's too reactive enough to attempt to use impact as a manner of mixing.
There has been several "odd" highly reactive Al powders. Frankly I think some of the tragedies may have been a result of those. The Teflon / Al powder
was really a death mix as was the commercial Al powder that had an adulterant of brass powder in it. (copper and a per / chlorate is a serious issue).
When the CPSC first put the clamp down the prices went from 4-8 USD a pound to $15 & there was a lot of money to be made. But when the final civil
action looked like it was going to hold, that was when people started to make fast money from it.
[Edited on 10-12-2010 by quicksilver]
|
|
Armistice19
Hazard to Self

Posts: 87
Registered: 19-6-2007
Member Is Offline
Mood: Brain sponge activated!
|
|
Free Reading.
The Wizard Is In, Thanks for the book info. I already found a free copy of "Mechanical Alloying And Milling" on Scribd.com
http://www.scribd.com/doc/3629131/Mechanical-alloying-and-mi...
Excellent reading material!!
As I mentioned earlier I had found my lead media to be deformed and chunky, also the mix was very warm after milling. I'm not sure about it but page
43 talks about deformation of powders due to heat caused by kinetic energy. I think this might explain the particular incident.
"Temperature rise during milling The intense mechanical deformation experienced by the powders leads to generation of crystal defects and this plus
the balance between cold welding and fracturing operations among the powder particles is expected to a€ect the structural changes in the
powder. Another important parameter, the temperature experienced by the powder during milling, dependent on the kinetic energy of the balls, can also
determine the nature of the final powder product. If the temperature generated is high, the associated higher di€usivity (higher atomic
mobility) leads to processes resulting in recovery (and recrystallization). In such a case, a stable phase, e.g., an intermetallic, would form. On the
other hand, if the temperature is low, then defect recovery would be less and an amorphous (or a nanocrystalline) phase would form. The temperature of
the powders during milling can be high due to two di€erent reasons. Firstly, as mentioned above it is due to the kinetic energy of the
grinding medium. Secondly, it is possible that exothermic processes occurring during the milling process generate heat. But, in practice, when the
temperature of the powder or the milling container is measured, it is probably due to a combination of these two factors. Additionally, one can
intentionally raise the temperature of the container, but this would not be considered here. Let us now consider the temperature rise during MA, due
to the kinetic energy of the grinding medium, either observed experimentally or calculated using some appropriate theoretical models. The intentional
raising of powder temperature to study the structural changes in the mechanically alloyed powder has been partially discussed in Section 4.3.10 and
will be further discussed in the individual sections on Solid Solubility Extensions, Intermetallic Phase Formation, Amorphous Phases, and
Nanostructures. A comprehensive review on the temperature e€ects during mechanical attrition has been prepared by Koch [203], which also
contains details of the different models used for these calculations. The macroscopic temperature of the vial (or powder) has been measured with
thermocouples in some cases. A maximum temperature of 40±428C was recorded [203] when the experiments were conducted with no balls in the container;
even with 13 balls in the SPEX mill, the temperature rise was noted to be only about 508C. Hence, it was concluded that most of the temperature rise
comes from the motor and bearings. Some investigators have, however, reported very large temperature rises. The data available on the measured
temperatures is summarized
in Table 6."
(Click the Link and scroll to page 44 to view the table)
It seems conventional ball mills can reach up to 90 degrees C. That sounds about right since my media and powder were very warm to the touch after
milling. I may reduce the amount of media in order to lighten the load. This in turn should cool down the motor, also using chrome plated steel media
should create less kinetic energy. Hopefully this second go round will turn out beautifully.
[Edited on 13-12-2010 by Armistice19]
“Imagination is more important than knowledge. For knowledge is limited to all we now know and understand, while imagination embraces the entire
world, and all there ever will be to know and understand.” -Albert Einstein
|
|
Pages:
1
2
3 |
|