Pages:
1
..
3
4
5
6 |
Hennig Brand
International Hazard
   
Posts: 1284
Registered: 7-6-2009
Member Is Offline
Mood: No Mood
|
|
Yes, if PIB is used (especially high MW PIB) then I think a solvent is pretty much a necessity to achieve even mixing and coating of the solid
explosive particles. Regarding oil types used, in many cases there is a big difference in the vapor pressures of the different oils available. Oil
with a lower vapor pressure will evaporate more slowly, meaning the plastique won't dry out as quickly. Also I imagine relative solubility, especially
with regards to temperature change, of the solid explosive in the various oils is important; recrystallization of the solid explosive and the
resultant hardening of the plastiques could be faster or slower depending on the oil used I would imagine (I haven't really done any testing though).
There are also viscosity differences to consider, especially with regards to temperature change. There are most likely a few other things I haven't
thought of as well.
"A risk-free world is a very dull world, one from which we are apt to learn little of consequence." -Geerat Vermeij
|
|
Laboratory of Liptakov
International Hazard
   
Posts: 1339
Registered: 2-9-2014
Location: Technion Haifa
Member Is Offline
Mood: cool.gif
|
|
Dent Plate
Henning, perfect work. Good idea to use double steel. But this method is very inaccurate. Yes, I know it was just a fun experiment. It is perhaps a
pity. You have the opportunity to get aluminum? The picture is a method that is used professionally. It is very simple. His name is dent plate. Lead,
copper and steel are not suitable metals.
You have 2 holes in steel. Where is the rest energy? This is very inaccurate. Dent plate is an exact method. Into aluminum discharged all the energy.
The depth of impact corresponds to the velocity of detonation.
LL
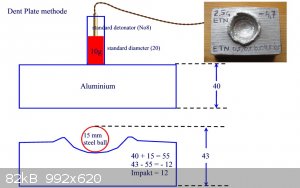
[Edited on 30-10-2014 by Laboratory of Liptakov]
|
|
Laboratory of Liptakov
International Hazard
   
Posts: 1339
Registered: 2-9-2014
Location: Technion Haifa
Member Is Offline
Mood: cool.gif
|
|
VoD
Other experiences include:
|
|
Hennig Brand
International Hazard
   
Posts: 1284
Registered: 7-6-2009
Member Is Offline
Mood: No Mood
|
|
Yes, I do normally have access to aluminum. I tend to use as targets anything that is lying around, so the targets are usually less than perfect.
Thanks for the good explanation.
I think all of those other metals have been used at one time or another as witnesses in various tests however. It wasn't a very accurate test I
performed, but a lot could be known about the relative detonation velocities based on the size of the holes and how clean the holes were (amount of
tearing and how much the steel was dented).
I like that last picture you posted, with the steel witness plate. Tells a lot about the detonation velocity of the 10% NG dynamite type explosive I
tested in the detcord thread. According to the literature I reviewed weeks ago, those types of explosives do have very low detonation velocities
(2000-3000m/s), which is consistent with your diagram.
[Edited on 30-10-2014 by Hennig Brand]
"A risk-free world is a very dull world, one from which we are apt to learn little of consequence." -Geerat Vermeij
|
|
Laboratory of Liptakov
International Hazard
   
Posts: 1339
Registered: 2-9-2014
Location: Technion Haifa
Member Is Offline
Mood: cool.gif
|
|
VoD
I'm glad that the pictures helped. Images are simple. As the graph and guidance for VoD calculation is inaccurate. However, if it agrees with your
experience, that's good. Here in this picture is a different situation. Only 4 grams of high explosive 6500m/s and 7500 m/s. Steel plate 3mm.
Interesting. Diameter expl. of 15mm. Hole of 15mm. Initiation No.10.
LL
|
|
Hennig Brand
International Hazard
   
Posts: 1284
Registered: 7-6-2009
Member Is Offline
Mood: No Mood
|
|
That is interesting; very different results. Much cleaner hole in the higher velocity shot. It gives me something to compare to which is nice. It
looks like that ETN putty explosive I have been playing with has higher detonation velocity than I thought it had (when properly initiated).
"A risk-free world is a very dull world, one from which we are apt to learn little of consequence." -Geerat Vermeij
|
|
Laboratory of Liptakov
International Hazard
   
Posts: 1339
Registered: 2-9-2014
Location: Technion Haifa
Member Is Offline
Mood: cool.gif
|
|
VoD
According shaped charges (octopus? Pyramid?) I think that: 1 about 6700 m/s and 2 about 7500 to 7900 m/s. The charge has a weak edge. It is difficult
to determine. The cylinder is much easier to determine.
LL
|
|
Hennig Brand
International Hazard
   
Posts: 1284
Registered: 7-6-2009
Member Is Offline
Mood: No Mood
|
|
I had a cone shape or truncated cone shape in the back of my mind, but when forming it quickly by hand I think I fell a little short of the correct
geometry.
To get the shape formed correctly a mold or form of some kind would have worked better. If the velocities are really that high, I am very impressed.
"A risk-free world is a very dull world, one from which we are apt to learn little of consequence." -Geerat Vermeij
|
|
Bert
Super Administrator
       
Posts: 2821
Registered: 12-3-2004
Member Is Offline
Mood: " I think we are all going to die. I think that love is an illusion. We are flawed, my darling".
|
|
Regarding "dent plate method":
Aluminum comes in a variety of alloys and hardness, T-0 to T-7 hardness is commonly available here...
What alloy/hardness would you choose for that 40mm plate/10gram charge you diagram?
I take it a plate of sufficient thickness not to "bulge" on back side is desired? From your practical experience, how thick might that need to be for
some typical materials, weight of charge & charge diameters-
Rapopart’s Rules for critical commentary:
1. Attempt to re-express your target’s position so clearly, vividly and fairly that your target says: “Thanks, I wish I’d thought of putting it
that way.”
2. List any points of agreement (especially if they are not matters of general or widespread agreement).
3. Mention anything you have learned from your target.
4. Only then are you permitted to say so much as a word of rebuttal or criticism.
Anatol Rapoport was a Russian-born American mathematical psychologist (1911-2007).
|
|
Laboratory of Liptakov
International Hazard
   
Posts: 1339
Registered: 2-9-2014
Location: Technion Haifa
Member Is Offline
Mood: cool.gif
|
|
test
For 10 g charge with minimum 40 mm thick. Another important thing: Height = 3x diameter cartridges. For relevant results. That is the minimum.
Hardness Aluminium 3 to 4 Medium. The bulge on the other side is not important. (see. fig.) The hardness of the aluminum is not too important.
Important are the same test conditions. For the known detonation velocity (pressure) and an unknown detonation velocity / pressure.
|
|
Hennig Brand
International Hazard
   
Posts: 1284
Registered: 7-6-2009
Member Is Offline
Mood: No Mood
|
|
Thanks, I will give that a try the next time I do a test.
"A risk-free world is a very dull world, one from which we are apt to learn little of consequence." -Geerat Vermeij
|
|
Laboratory of Liptakov
International Hazard
   
Posts: 1339
Registered: 2-9-2014
Location: Technion Haifa
Member Is Offline
Mood: cool.gif
|
|
methyl ricinoleate
I want to return to the topic of high density. Henning has a great knowledge of plasticizers. I read the entire thread. I see that the polybutylene is
better than polyisobutylene. A little bit better? Or much better? Another question: How to make methyl ricinoleates? I know that it's almost like
adipate and sebacate. It is important, in fact necessary ingredient in plasticizer.
He could make anyone of you methyl ricinoleate? I have methanol, castor oil, KOH and NaOH. Thank you, LL
|
|
Hennig Brand
International Hazard
   
Posts: 1284
Registered: 7-6-2009
Member Is Offline
Mood: No Mood
|
|
Thanks for the compliment, but I am still just getting the basics about a lot of this stuff. It is better and worse. The product I have is very easily
incorporated into a plastic/putty explosive without the use of a solvent, which saves a lot of work. This strength is also a weakness; it doesn't hold
the explosive particles together as well as a higher molecular weight/longer average chain length polymer/binder. In order to compensate more binder
is used and then it does make a decent plastique if done right. I don't think there is a one size fits all; the binder and plasticizer choice depend
on the handling properties one wants in a plastic explosive.
"A risk-free world is a very dull world, one from which we are apt to learn little of consequence." -Geerat Vermeij
|
|
Metacelsus
International Hazard
   
Posts: 2531
Registered: 26-12-2012
Location: Boston, MA
Member Is Offline
Mood: Double, double, toil and trouble
|
|
Making methyl esters of fatty acids is commonly done by people making biodiesel from vegetable oil. Castor oil is mostly the triglyceride ester of
ricinoleic acid, so you can use base-catalyzed transesterification. Look on biodiesel sites for more details.
Here's a paper about castor oil biodiesel: http://www.icrepq.com/full-paper-icrep/222-barajas.pdf
[Edited on 23-11-2014 by Cheddite Cheese]
|
|
NeonPulse
Hazard to Others
 
Posts: 417
Registered: 29-6-2013
Location: The other end of the internet.
Member Is Offline
Mood: Isolated from Reality! For Real this time....
|
|
I have made methyl ricinoleate and it works far better than oil alone. And polybutene seems to work better than pib.it seems less brittle and easily
worked back to softness upon sitting for a while.having never used adipates or sebecates I can't comment on which is better but the ricinoleate is
pretty darn good and easy to make. Its a quite simple reaction really.
|
|
roXefeller
Hazard to Others
 
Posts: 463
Registered: 9-9-2013
Location: 13 Colonies
Member Is Offline
Mood: 220 221 whatever it takes
|
|
It is straight forward, like making soap. In fact I made soap once doing this because of bad temperature control. I've attached the article I
followed (they were experimenting with conditions and catalyst concentration). One thing I found helpful was to have all reagents at the reaction
temperature before combining. After allowing time to react, stir in water to separate the glycerol and byproducts from the ester.
Attachment: methylricinoleate.pdf (42kB) This file has been downloaded 584 times
|
|
Hennig Brand
International Hazard
   
Posts: 1284
Registered: 7-6-2009
Member Is Offline
Mood: No Mood
|
|
Methyl ricinoleate does work and most importantly it is available to the hobbyist. Seems to me that methyl ricinoleate is not in favor, as a
plasticizer, for most commercial applications however. I would have to go do a little digging, but IIRC it had much poorer storage stability than the
ones typically used commercially.
"A risk-free world is a very dull world, one from which we are apt to learn little of consequence." -Geerat Vermeij
|
|
Laboratory of Liptakov
International Hazard
   
Posts: 1339
Registered: 2-9-2014
Location: Technion Haifa
Member Is Offline
Mood: cool.gif
|
|
methylricinoleate
roXfeller, thank you for pdf .. I suggest the following: 250 ml ricin oil + 65 ml methanol + 2.4 g KOH. Keep temperature at 70C for 90 minutes. Yield:
95 ml methylricinoleate + 42 ml glycerol. We can only try. LL
|
|
markx
National Hazard
  
Posts: 645
Registered: 7-8-2003
Location: Northern kingdom
Member Is Offline
Mood: Very Jolly
|
|
For the transesterification of (castor) oil, one important element is to keep the content of catalyst (KOH or NaOH) to a rather minimum amount (at
least not exceeding the amount suggested in the synthesis description). Higher concentrations of the base tend to favour saponification reactions.
Especially if the alcohol is not of fully anhydrous composition.
Exact science is a figment of imagination.......
|
|
NeonPulse
Hazard to Others
 
Posts: 417
Registered: 29-6-2013
Location: The other end of the internet.
Member Is Offline
Mood: Isolated from Reality! For Real this time....
|
|
The gelatinous mess was the result of my 1st attempt. And it was due to too much catalyst as well as poor temp control. Future reactions were much
more successful with the right product yielded.
|
|
markx
National Hazard
  
Posts: 645
Registered: 7-8-2003
Location: Northern kingdom
Member Is Offline
Mood: Very Jolly
|
|
For the comparison of PIB and polybutylene binders...I find that if a classical plastique type of product is desired then HMW PIB does give a better
result in terms of consistancy and the mass really holds together very well. But it does require a fair amount of plastisizer (methyl riccinoleate
e.g) to be reasonably moldable. If less is added the mass becomes quite tough and rubbery. Polybutylene on the other hand yields a softer stickier
product which crumbles quite easily, but is near too perfect for phlegmatisation of SC loads in the 5%-10% inerts range. I've used 5% of
polybutylene+5% methyl riccinoleate on PETN and RDX based SC loads and it gives excellent loading properties....good density and uniformity without
excessive pressing. And just enough adhesion to form a solid charge that grips the casing and liner very well.
[Edited on 25-11-2014 by markx]
Exact science is a figment of imagination.......
|
|
Laboratory of Liptakov
International Hazard
   
Posts: 1339
Registered: 2-9-2014
Location: Technion Haifa
Member Is Offline
Mood: cool.gif
|
|
plasticizer
Interesting post markx. To refresh your memory. C4:
RDX ................................................. .. 91.0%
Di (2-ethylhexyl) sebacat ........................ 5.3%
Polyisobutylene ....................................... 2.1%
oil (synthetic 5W?) .................................. 1.6%.
This is not many (9%) of a plasticizer. Usually (often) it is 15%. Q: Is it possible to replace Di (2-ethylhexyl) sebacat, methyl ricinoleate? If yes.
Also use the 5.3%? I know that C4 is not (much) the plastic explosive. Semtex is more plastic. But he has a lot of plasticizer. (19?) Markx: You're
only used 5% plasticizer? Or 5% polybutylene and 5% methyl ricinoleate? Thank you, LL .............
|
|
markx
National Hazard
  
Posts: 645
Registered: 7-8-2003
Location: Northern kingdom
Member Is Offline
Mood: Very Jolly
|
|
Quote: Originally posted by Laboratory of Liptakov  |
Interesting post markx. To refresh your memory. C4:
RDX ................................................. .. 91.0%
Di (2-ethylhexyl) sebacat ........................ 5.3%
Polyisobutylene ....................................... 2.1%
oil (synthetic 5W?) .................................. 1.6%.
This is not many (9%) of a plasticizer. Usually (often) it is 15%. Q: Is it possible to replace Di (2-ethylhexyl) sebacat, methyl ricinoleate? If yes.
Also use the 5.3%? I know that C4 is not (much) the plastic explosive. Semtex is more plastic. But he has a lot of plasticizer. (19?) Markx: You're
only used 5% plasticizer? Or 5% polybutylene and 5% methyl ricinoleate? Thank you, LL ............. |
Good remark...I was unclear in my last post, mind rushed ahead of the fingers. Sometimes I tend to forget that the readers can not read minds...only
the text
So yes, I used 5% polybutylene + 5% methyl riccinoleate for the shaped charge phlegmatisation purpose:
9g PETN/RDX
1g plastification mixture
plastification mixture: 50/50% by mass methyl riccinoleate/polybutylene
The sebacate in the original C4 composition can be replaced by the methyl riccinoleate. As for the exact ratio I do not know...one can start off with
a 1:1 ratio and work ahead from there in either direction until a satisfactory result is obtained. I do not think though that the 1:1 replacement
ratio happens to be the optimum one.
As I understand cyclonite tends to suffer significant losses in VoD and cap sensitivity if more than 10% inerts are incorporated into the mix...hence
the 9% inerts content of the C4 composition and the "not so plastic" consistancy. In that sense PETN is way more forgiving and allows to work upwards
of 20% inert content of formulations without significant limitations in either VoD nor cap sensitivity.
Exact science is a figment of imagination.......
|
|
Laboratory of Liptakov
International Hazard
   
Posts: 1339
Registered: 2-9-2014
Location: Technion Haifa
Member Is Offline
Mood: cool.gif
|
|
methylricinoleate
Oh, thank you, absolutely perfect answer. Everything was written true and legible letters and words. No secret thoughts were observed. In this
situation it is clear that methyl-ricin-oleate will soon be manufactured and tested. LL .....
|
|
ecos
Hazard to Others
 
Posts: 464
Registered: 6-3-2014
Member Is Offline
Mood: Learning !
|
|
Hi,
I found this method to make high density blasting gel : Link
|
|
Pages:
1
..
3
4
5
6 |