Pages:
1
2
3 |
sinai
Harmless
Posts: 10
Registered: 10-8-2011
Member Is Offline
Mood: No Mood
|
|
Aluminium foil to Aluminium Oxide?
Firstly, I want to know if the product from this is Al2O3 (Aluminium Oxide):
I took a piece of Aluminium foil and lightly crumbled it into a ball. I weighed the Al foil ball, it was 0.334g. I then torched the Al ball with
propane until near destruction, the aluminium foil shrunk and changed colour to a more dull grey metallic surface. Once cooled, I weighed the now
smaller and harder Al ball and the weight was 0.38g, an increase of 0.044g which I beleive is due to oxidation. Is the product aluminium oxide? Or a
partial oxidation?
Secondly, what is a good 1step method to create aluminium oxide from aluminium foil with a high grade yield? I already know of the aluminium and NaOH
to create aluminium hydroxide is then heat until it decomposes to aluminium oxide; < which I think is one step too many.
I appreciate any input. And thanks for reading.
"Speak good, Behave good, and See good" - Ahura Mazda
|
|
not_important
International Hazard
   
Posts: 3873
Registered: 21-7-2006
Member Is Offline
Mood: No Mood
|
|
Al2O4 is the only stable oxide around STP, so "partial oxidation" would mean having unreacted Al metal. Calculated what weight of Al2O3 you should
get with 100% reaction and compare.
And that's the problem - the oxide layer does a good job at protecting the underlying metal that it's difficult to get full conversion. You'd do
better finding some Al2(SO4)3 in a garden supply store and precipitating the hydroxide using NaOH, Na2CO2, NaHCO3, or even aqueous ammonia. The
product will be purer as well, most metallic Al is some alloy or other.
[Edited on 18-8-2011 by not_important]
|
|
condennnsa
Hazard to Others
 
Posts: 217
Registered: 20-4-2010
Location: Romania
Member Is Offline
Mood: No Mood
|
|
I've read lots of times on the internet about people making 'aluminum oxide' by heating foil or al cans with a blowtorch, but it just does not work,
like not_important said the oxide layer passivates the aluminum very well even at temperatures well above the melting point of Al.
What I think happens is that the metal as it becomes molten flows down from between the two aluminum oxide "shells", this is why after heating you are
left with a crumbly thing of what seems to be Al2O3.
Since you mentioned the sodium hydroxide method, I am really fascinated by that reaction, because I once tried it with a very concentrated solution of
NaOH and what happened is that no matter how much Aluminum I would add to it, it would keep on reacting , and the liquid became thicker and thicker
because of the Al(OH)3 ? slurry. I must have reacted about 400-500g of aluminum in about 50-60g of NaOH.
On the other hand when I used a very dilute solution of NaOH, the reaction would pretty soon stop, and no Al(OH)3 precipitate being formed.
So I think that above a certain pH, the sodium aluminate decomposes to NaOH and Al(OH)3 ??
Is this correct? has any of the more experienced members here done this experiment?
|
|
Endimion17
International Hazard
   
Posts: 1468
Registered: 17-7-2011
Location: shores of a solar sea
Member Is Offline
Mood: speeding through time at the rate of 1 second per second
|
|
condennnsa is right, any aluminum left is sandwiched between two layers of very thin oxide, and it can not be oxidized further by that method.
Aluminum foil burning was always a lousy way of getting the oxide.
There's one interesting thing that shows up when the foil is being heated in different flame zones. Colors appear, similar to ones anodizing produces,
and showing that indeed there are oxide layers of different thicknes being produced, although all of them are ridiculously thin compared to the
thickness of the foil.
|
|
sinai
Harmless
Posts: 10
Registered: 10-8-2011
Member Is Offline
Mood: No Mood
|
|
Yeah, I guess the oxide layers just increased, but still a sandwicch.
@not important : yeah I want to buy some, but I've seen brown, white, see through and metallic powders all being called aluminum oxide. Guess some are
not as pure as the others. But if there is an easy quick method of making it from Al foil, the price difference would justify it, in the uk anyway.
@condensa : it depends how much al you have, the best way is to use as little water as possible and add the NaOH to the al slowly with water present
until a reaction proceeds. And yes PH has something to do with the initiation, but I would say with the dilute NaOH, it was happening very slowly, and
perhaps you didn't notice the reaction.
@endimion : yeah.. funny enough, iron oxide and aluminium powder form termite, even though the al powder still has an oxide layer.
"Speak good, Behave good, and See good" - Ahura Mazda
|
|
Retard-3000
Hazard to Self

Posts: 55
Registered: 17-11-2010
Member Is Offline
Mood: No Mood
|
|
4Al + 3O2 > 2Al2O3
0.33g of Aluminium should oxidize completely to 0.62g of Aluminium Oxide, However, you only have 0.38g of Al/Al2O3 showing that it hasn't been fully
oxidized.
|
|
blogfast25
International Hazard
   
Posts: 10562
Registered: 3-2-2008
Location: Neverland
Member Is Offline
Mood: No Mood
|
|
Dissolve the foil in 50 % NaOH or KOH (allow a small stoichiometric excess), to form aluminate (NaAl(OH)4), filter solution, if deemed necessary.
Simmer to increase reaction speed, if needed.
After cooling, carefully neutralise with about 20 % H2SO4, till close to pH 7. Good pH control is needed to prevent the oxide from redissolving.
Gelatinous Al(OH)3.nH2O drops out. Filter and wash filter cake carefully with several small aliquots of clean water. Filtrate contains valuable Na2SO4
(or K2SO4) and can be recovered. Dry the hydrated alumina till constant weight at about 150 - 200 C. Technical Al2O3 is now yours. For certain uses,
calcine properly.
[Edited on 18-8-2011 by blogfast25]
|
|
sinai
Harmless
Posts: 10
Registered: 10-8-2011
Member Is Offline
Mood: No Mood
|
|
@Retard-3000 - yeah, your calculations are correct, I kind of guessed my experiments weight increase was minuscule. But I wanted to double check if it
was al oxide, you never know, maybe unburnt propane itself fused with the al :-P Thanks for the calculation.
@blogfast25 thanks, going totry it out. By the way, do you have any idea on how to chemically form al powder?
"Speak good, Behave good, and See good" - Ahura Mazda
|
|
blogfast25
International Hazard
   
Posts: 10562
Registered: 3-2-2008
Location: Neverland
Member Is Offline
Mood: No Mood
|
|
Quote: Originally posted by sinai  | @blogfast25 thanks, going totry it out. By the way, do you have any idea on how to chemically form al powder? |
The most technologically advanced method involves turning liquid aluminium into an aerosol (but in argon gas) by pumping it through a suitable nozzle.
Good luck with that!
Ball milling appears difficult but possible.
The most affordable method for the amateur is grinding a block of aluminium under water on a turning grinding stone or drum covered with sanding
paper. There are designs for such machines published by hobbyists on the Net. Google and yee shall find!
There are no chemical means of doing this, AFAIK.
[Edited on 18-8-2011 by blogfast25]
|
|
AJKOER
Radically Dubious
   
Posts: 3026
Registered: 7-5-2011
Member Is Offline
Mood: No Mood
|
|
A home chemist preparation based on one of my threads is:
1. Pre-soak Al foil with vinegar for a few hours. This makes subsequent chemical attack on the foil more efficient. I got this from a website where an
Aluminum coating manufacturer that lamented over the ability of vinegar to bypass their resistant/hardening efforts on Al foil. Note, if acidic food
can easily react with Al, there would be a health issue with Aluminum (assuming there isn't one already).
2. Let treated Al foil slowly dissolve overnight in household ammonia. Depending on your foil, some Silicon (a black solid) will remain.
Actually, the chemistry is that the NH3 dissolves the Al2O3 and then water reacts with the pure exposed Al liberating H2 and forming Al(OH)3, which is
gelatinous.
------------------------------
On forming highly reactive Al from solution, I would think one might make a water free Aluminum salt and dissolve in an appropriate organic solvent.
Then, react with another metal via a displacement reaction to liberate the Aluminum, may be a path.
[Edited on 18-8-2011 by AJKOER]
[Edited on 18-8-2011 by AJKOER]
|
|
Bezaleel
Hazard to Others
 
Posts: 444
Registered: 28-2-2009
Member Is Offline
Mood: transitional
|
|
Quote: Originally posted by AJKOER  |
2. Let treated Al foil slowly dissolve overnight in household ammonia. Depending on your foil, some Silicon (a black solid) will remain.
Actually, the chemistry is that the NH3 dissolves the Al2O3 and then water reacts with the pure exposed Al liberating H2 and forming Al(OH)3, which is
gelatinous.
|
If that is really so, then what are the reaction products? I'm amazed to hear aluminium would dissolve in ammonia, as eating through the oxide layer
in strong NaOH already takes a few minutes.
|
|
condennnsa
Hazard to Others
 
Posts: 217
Registered: 20-4-2010
Location: Romania
Member Is Offline
Mood: No Mood
|
|
Quote: Originally posted by Bezaleel  |
If that is really so, then what are the reaction products? I'm amazed to hear aluminium would dissolve in ammonia, as eating through the oxide layer
in strong NaOH already takes a few minutes. |
Strong NaOH takes seconds to do that
Another method to make alumina from Al would be by electrolysis, an aluminum anode in NaCl solution will quickly disappear to Al(OH)3 ...
[Edited on 18-8-2011 by condennnsa]
|
|
AJKOER
Radically Dubious
   
Posts: 3026
Registered: 7-5-2011
Member Is Offline
Mood: No Mood
|
|
Bezaleel:
As was correctly noted by Blogfast25, Aluminum quickly dissolves in NaOH to form Sodium aluminate (formula: NaAl(OH)4 ) and not Al(OH)3. This
potentially violent reaction (not referring to Blogfast25's recipe) also produces hydrogen gas. One then must also carefully neutalize (also
dangerous) with H2SO4 to form the Al(OH)3 and avoid re-dissolving. These are caustic chemicals that you may or may not have on hand.
On the other hand, with my procedure one can avoid any neutralizing as the NH3 just evaporates. You can also avoid trying to filter the jelly by hand
pouring out most of the solution, leaving the gelatinous Aluminum hydroxide and add distilled H2O to wash. When done washing, just leave the Al(OH)3
in an open dish to evaporate.
The hydrolysis of Al in H2O (after the removal/penetration of the Al2O3 with ammonia) proceeds as follows:
2 Al + 6 H2O --> 2 Al(OH)3 + 3 H2
Now as to the dissolving of Al2O3 in NH4OH, there is some controversy as to its description as either Ammonium aluminate (only limited indirect
support for its existence) or, more likely, an ammonia peptized Al(OH)3 gel.
I personally save my NaOH (and not to mention H2SO4) for something more interesting like making ferrates.
[Edited on 18-8-2011 by AJKOER]
[Edited on 18-8-2011 by AJKOER]
[Edited on 19-8-2011 by AJKOER]
|
|
blogfast25
International Hazard
   
Posts: 10562
Registered: 3-2-2008
Location: Neverland
Member Is Offline
Mood: No Mood
|
|
AJKOER:
STOP PEDDLING RIDICULOUS NONSENSE ON THIS FORUM.
The method I use isn’t only not dangerous (with you everything is dangerous!!!), it works very well. Even with 50 % KOH aluminium foil or cuttings
DON’T react ‘violently’, in fact it takes time and some gentle heat. And if you can’t handle caustic soda, please take up PHILATELY, or
KNITTING…
Ammonia solution DOES NOT FORM aluminates in significant quantities.
STOP PEDDLING DAMN LIES.   
|
|
White Yeti
National Hazard
  
Posts: 816
Registered: 20-7-2011
Location: Asperger's spectrum
Member Is Offline
Mood: delocalized
|
|
The best way I know to make alumina at a reasonlably large scale is... thermite. Try getting your hands on some thermite and put it into a refractory
crucible. If you can, drill some holes into the bottom of the crucible so that some of the molten iron can flow out. Obviously, it's a good idea to
put a container underneath to catch the molten metal. Once the reaction mix is cool, grind it into powder by any means necessary. Alumina is a ceramic
that will crumble into a powder while iron is a ductile metal that won't crumble, so you can separate iron bits and pieces with a magnet at this
point. For extra purity, you can dump the powder into some HCl, this will get rid of both Al and Fe, making them soluble. Once the powder stops
bubbling, filter the mixture and dry. You are now the proud owner of pure aluminum oxide
|
|
blogfast25
International Hazard
   
Posts: 10562
Registered: 3-2-2008
Location: Neverland
Member Is Offline
Mood: No Mood
|
|
Quote: Originally posted by White Yeti  | The best way I know to make alumina at a reasonlably large scale is... thermite. Try getting your hands on some thermite and put it into a refractory
crucible. If you can, drill some holes into the bottom of the crucible so that some of the molten iron can flow out. Obviously, it's a good idea to
put a container underneath to catch the molten metal. Once the reaction mix is cool, grind it into powder by any means necessary. Alumina is a ceramic
that will crumble into a powder while iron is a ductile metal that won't crumble, so you can separate iron bits and pieces with a magnet at this
point. For extra purity, you can dump the powder into some HCl, this will get rid of both Al and Fe, making them soluble. Once the powder stops
bubbling, filter the mixture and dry. You are now the proud owner of pure aluminum oxide |
If you're going the thermite route, simple do KClO3 + 2 Al --- KCl + Al2O3. I use this mixture as 'ignition mix' for most pyrometallurgical
experiments because it ignites just about any thermite or analog.
That mixture burns so hot that the KCl completely evaporates.
Trouble is that what you obtain is annealed alumina and for most home chemists that's useless: trying to dissolve that is like trying to
dissolve corundum: extremely difficult. It's also very hard mechanically speaking: almost impossible to size reduce by hobbyists.
I have a collection of thermite 'left overs' (shells of annealed alumina) and even bashing them with a hammer has almost no effect.
To purify alumina from real thermites is in my experience basically impossible unless you have a way to micronise this extremely hard material...
[Edited on 18-8-2011 by blogfast25]
|
|
White Yeti
National Hazard
  
Posts: 816
Registered: 20-7-2011
Location: Asperger's spectrum
Member Is Offline
Mood: delocalized
|
|
Quote: Originally posted by blogfast25  | If you're going the thermite route, simple do KClO3 + 2 Al --- KCl + Al2O3. I use this mixture as 'ignition mix' for most pyrometallurgical
experiments because it ignites just about any thermite or analog.
That mixture burns so hot that the KCl completely evaporates.
Trouble is that what you obtain is annealed alumina and for most home chemists that's useless: trying to dissolve that is like trying to
dissolve corundum: extremely difficult. It's also very hard mechanically speaking: almost impossible to size reduce by hobbyists.
I have a collection of thermite 'left overs' (shells of annealed alumina) and even bashing them with a hammer has almost no effect.
|
I didn't think of that, but you're absolutely right, that method would give you a tough mass of annealed aluminium oxide. You could probably use it to
make tank armour 
I thought the OP wanted to have some alumina powder, not an indestructable lump. Although I'm not sure if thermite would also yield an indestructable
annealed lump as well. It's been a while since I set off my last thermite, so I don't remember.
|
|
blogfast25
International Hazard
   
Posts: 10562
Registered: 3-2-2008
Location: Neverland
Member Is Offline
Mood: No Mood
|
|
Quote: Originally posted by White Yeti  | I didn't think of that, but you're absolutely right, that method would give you a tough mass of annealed aluminium oxide. You could probably use it to
make tank armour 
I thought the OP wanted to have some alumina powder, not an indestructable lump. Although I'm not sure if thermite would also yield an indestructable
annealed lump as well. It's been a while since I set off my last thermite, so I don't remember. |
In my book (I've 'thermited' oxides of Fe, Si, Ti, Cr, Mn, V, Nb, Cu and some alloys too) a well designed thermite formulation yields good quality
metal, well separated from the nuissance by-product, alumina. To achieve this, the mixture has to be designed to reach well above the MP of alumina,
otherwise no separation between metal and slag (alumina) can occur. So the alumina, all being well, forms in the molten state (as does the metal) and
gravity and immiscibility then cause the metal to separate out and sink to the bottom of the slag puddle. Both metal and slag then solidify, the slag
forming annealed alumina. Hard as corundum, trust me. I might post a few photos of these alumina shells here later on.
|
|
AJKOER
Radically Dubious
   
Posts: 3026
Registered: 7-5-2011
Member Is Offline
Mood: No Mood
|
|
Blogfast25:
As usual you fail to qualify your reputed knowledge.
I have performed this very reaction many years ago using NaOH flakes and Al pieces. The ingedients were directly from a Drano can intended to clear
drains. If it was not a voilent reaction in concentrated form, generating both heat and gas as I observed, Drano would probably not work! You should
have read the label warning.
Now, I do not necessarily doubt that your NaOH may act differently as we are discussing different concentrations and possibly also quality issues.
However, unlike you, I do not assume everyone understands the dangers of working with strong bases and acids, and to critize someone who values safety
on a public forum based on experience is inappropriate to say the least.
On the Ammonia aluminate, you have the literature as I gave it to you, and my comment was completely in keeping with it, to quote "only limited
indirect support for its existence) or, more likely, an ammonia peptized Al(OH)3 gel"
.
|
|
sinai
Harmless
Posts: 10
Registered: 10-8-2011
Member Is Offline
Mood: No Mood
|
|
Thanks guys, and hope the heat is gone.
@condennsa, the electrolysis method sounds ideal.
@ajkoer, about some manufacturers being vary about acidic food is right,most foils are mixed with small amounts of silica and other things to minimize
the erosion/holes but would entirely depend on what brand/foil type.
@blogfast25 thermite/metals winning over other metals sounds great, I need to get myself some graphite and carbon based casts and experiment, but as
White yet said, most products are desired in powdered/high surface area form to be useful in lab scale chemistry. By the way, I was researching the
formation of nano sized particles of various metals incl. Al induced electrochemically. Thought I mention it in case it might interest your intellect.
Its funny though, how nature itself produced aluminium oxide in bauxite. The theory is there, but amazing.
And guys, stop arguing, and about safety, anyone who crosses the road without looking both ways first is to blame, not the guy who gave him the
directions.
"Speak good, Behave good, and See good" - Ahura Mazda
|
|
AJKOER
Radically Dubious
   
Posts: 3026
Registered: 7-5-2011
Member Is Offline
Mood: No Mood
|
|
Blogfast25:
I have edited my comments on your recipe as it was not my intention to imply that it is per se, a dangerous process.
I was, in fact, thinking of my personal experience with Drano.
Sorry.
|
|
Neil
National Hazard
  
Posts: 556
Registered: 19-3-2008
Member Is Offline
Mood: No Mood
|
|
Quote: Originally posted by AJKOER  | Blogfast25:
As usual you fail to qualify your reputed knowledge.
I have performed this very reaction many years ago using NaOH flakes and Al pieces. The ingedients were directly from a Drano can intended to clear
drains. If it was not a voilent reaction in concentrated form, generating both heat and gas as I observed, Drano would probably not work! You should
have read the label warning.
Now, I do not necessarily doubt that your NaOH may act differently as we are discussing different concentrations and possibly also quality issues.
However, unlike you, I do not assume everyone understands the dangers of working with strong bases and acids, and to critize someone who values safety
on a public forum based on experience is inappropriate to say the least.
On the Ammonia aluminate, you have the literature as I gave it to you, and my comment was completely in keeping with it, to quote "only limited
indirect support for its existence) or, more likely, an ammonia peptized Al(OH)3 gel"
. |
Drano is a mixture of Aluminium, Sodium Nitrate and Sodium Hydroxide. The idea is the aluminium and hydroxide react producing heat and hydrogen which
stirs and agitates. The nitrate combines with the hydrogen and converts it to ammonia which reduces the chance of explosion.
I've brought thermite alumina down to ~400mesh powders in an iron mortar and pestle. I've leached it and heated it and swore at it. Never did purify
it though.
Al2O3 IS used in tank armour 
I've tried burning Al down with fluxes, poor yield.
I've tried going the NaOH route but the effort to product and cost was to high for anything being reagent amounts.
Try looking for local pottery stores, or order it online for pottery.
I've used a electrolysis cell to break it down, it was the fastest and cheapest but venting the hydrogen was a concern. it produces a lot of heat, I
fed in scrap Al during the winter and used the heat to warm my room.
I'd also stay away from carbon crucibles if I were you, others may correct me but in my experience the molten Alumina is very effective at producing
alumina oxycarbides when given the chance.
|
|
blogfast25
International Hazard
   
Posts: 10562
Registered: 3-2-2008
Location: Neverland
Member Is Offline
Mood: No Mood
|
|
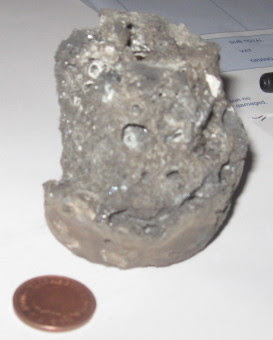
This is an example of thermite alumina but not a very good one. This silicon thermite, boosted with chlorate/Al powder, didn’t reach a high enough
temperature for the reaction product mix to collect at the bottom of the crucible, so a lot of it froze up on the way down. Despite its porous nature,
this little sculpture resists hammering down very well: it's much harder than many a common rock. In it are embedded ‘studs’ of silicon metal
(hard to see on the photo), one about a cm wide.
|
|
not_important
International Hazard
   
Posts: 3873
Registered: 21-7-2006
Member Is Offline
Mood: No Mood
|
|
Quote: Originally posted by AJKOER  |
As was correctly noted by Blogfast25, Aluminum quickly dissolves in NaOH to form Sodium aluminate (formula: NaAl(OH)4 ) and not Al(OH)3. This
potentially violent reaction (not referring to Blogfast25's recipe) also produces hydrogen gas. One then must also carefully neutalize (also
dangerous) with H2SO4 to form the Al(OH)3 and avoid re-dissolving. These are caustic chemicals that you may or may not have on hand.
On the other hand, with my procedure one can avoid any neutralizing as the NH3 just evaporates. ... |
Nope, don't need H2SO4 or HCl, CO2 will do the trick as will NaHCO3. Takes a powerful base to form aluminates, which is why using NH3(aq) doesn't
really do the job.
As said above, thermite leftovers are fused alumina - hard, unreactive, and contaminated with whatever metal was being reduced as well as anything
else around. Alumina targeted at abrasive use is also the fused variety, it dissolves in HF or fused NaOH. Pottery grade Al2O3 isn't much better,
even pottery grade Al(OH)3 can be slow to dissolve in HCl.
Which is why I suggested starting with agricultural/gardening grade Al sulfate and using one of the bases I listed to ppt out nice fresh Al(OH)3.
|
|
Bezaleel
Hazard to Others
 
Posts: 444
Registered: 28-2-2009
Member Is Offline
Mood: transitional
|
|
Quote: Originally posted by AJKOER  | On the Ammonia aluminate, you have the literature as I gave it to you, and my comment was completely in keeping with it, to quote "only limited
indirect support for its existence) or, more likely, an ammonia peptized Al(OH)3 gel" |
Maybe you could post the reference to literature that I may read the article myself? I'm amazed about amonia being capable of reacting with the oxide
layer in one way or another.
|
|
Pages:
1
2
3 |