blogfast25
International Hazard
   
Posts: 10562
Registered: 3-2-2008
Location: Neverland
Member Is Offline
Mood: No Mood
|
|
When NiChrome isn’t NiChrome?
I’ve messed around with quite a few alloys and quantitatively analysed some too but never NiChrome. So when the family hair drier clapped out
yesterday, I recovered the coiled heating elements, presuming they were probably NiChrome.
A few cm of coil was dunked in some 70 % HNO3 and… nothing happened, not even on heating. Passivation, no doubt. Adding some 37 % HCl got the
reaction going and the wire dissolved in a jiffy. I diluted slightly, then filtered (there was a small amount of acid insoluble residue), obtaining an
emerald green solution. So far, so good.
Then upon neutralising with 5 M NaOH, thick wads of a red/brown precipitate formed, clearly ferric hydroxide. Amm. rhodanide confirmed iron (III). I
filtered and washed this and the filtrate was clear and white.
Assuming there was chromium in this alloys all the same, the still wet filter cake was mixed with an arbitrary amount of KOH and some KClO3, then
‘fused’ for about 20 min on a high flame Bunsen, in a SS crucible.
After cooling water was added to the ‘frit’, then simmered for a bit, then filtrated. The filtrate, about 25 ml) ran a clear, urine yellow and
tested strongly positive for PbCrO4 with Pb(NO3)2 solution. Acidified with HCl the solution turned green when methanol and a bit of heat was added
(reduction to Cr3+). Clearly the filtrate contained quite a bit of potassium chromate (VI).
The green colour of the initial solution must be explained as yellow ferric ions plus blue/green chromic ions = green solution.
I couldn’t find any nickel in there but I haven’t yet looked that closely either.
|
|
watson.fawkes
International Hazard
   
Posts: 2793
Registered: 16-8-2008
Member Is Offline
Mood: No Mood
|
|
Quote: Originally posted by blogfast25  | So when the family hair drier clapped out yesterday, I recovered the coiled heating elements, presuming they were probably NiChrome.
| There are lots of resistance alloys out there. When there's no need to go to red heat or there's low duty
cycles, both of which are frequently the case for consumer applications, you can use cheaper alloys. There's a Fe-Cr-Al alloy, for example, with no Ni
at all. Even Ni-Cr is often used with Fe for such applications. The "nickel 60" alloy, for example, could be either Ni-60, Cr-40 or Ni-60, Cr-16,
Fe-24; I've seen both.
|
|
Morgan
International Hazard
   
Posts: 1660
Registered: 28-12-2010
Member Is Offline
Mood: No Mood
|
|
Tidbits
"A common alloy is 80% nickel and 20% chromium, by mass, but there are many others to accommodate various applications."
http://en.wikipedia.org/wiki/Nichrome
Nichrome-60 wire (NiCr60 Type Alloy 675 Nickel Chrome Alloy)
Nickel: 57-58%, Chromium: 16%, Silicon: 1.5%, Iron: Balance
http://www.heatersplus.com/nichrome.html
|
|
blogfast25
International Hazard
   
Posts: 10562
Registered: 3-2-2008
Location: Neverland
Member Is Offline
Mood: No Mood
|
|
Ooops. Double post. Not sure why.
[Edited on 26-8-2012 by blogfast25]
|
|
blogfast25
International Hazard
   
Posts: 10562
Registered: 3-2-2008
Location: Neverland
Member Is Offline
Mood: No Mood
|
|
Another heating element sample was obtained, this one 1.4 g from a broken electrical frier. Here the heating wire was embedded in ceramic, in turn
enclosed in an Al tube (quite a classic design) and it too appeared to be FeCr.
It dissolved readily in hot 36 % HCl, with almost no residue (suggesting also absence of Ni as the latter doesn’t dissolve well in HCl), to an
emerald green. To extract the Cr, I precipitated everything with an excess KOH (about 10 g), then chilled, then added 9 % H2O2 slowly to the slurry
and simmered for a few minutes. On filtering this solution of chromate eluted:
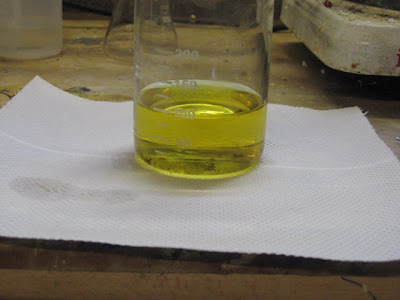
The filter cake was typical brown ferric hydoxide.
The chromate was chilled, then acidified with strong HCl (the colour change to dichromate is very significant), then chilled. 9 % H2O2 was then added
and the solution changes first to a deep blue then seconds later to the familiar green of Cr3+:
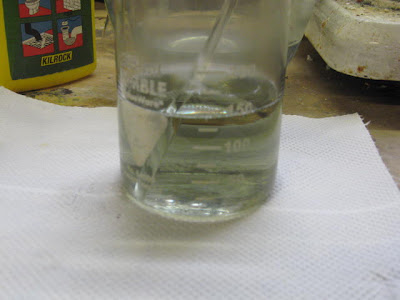
Could the blue flash indicate temporary reduction to Cr2+?
Then after some more manipulations, treatment with 30 % NH3 gave the interesting colour of the [Cr(NH<sub>3</sub> <sub>6</sub>]<sup>3+</sup> cation:
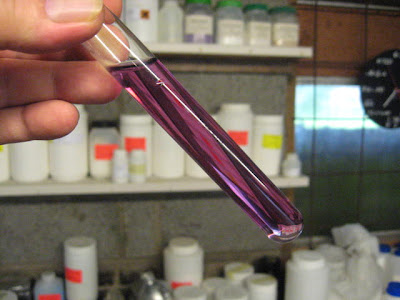
Question:
Does anybody have a ready-to–use titrometric determination of Cr<sup>3+</sup>?
I was thinking: reduce with Zn powder to Cr2+, then titrate with KMnO4 under CO2 blanket.
Or chelometry: back titrate excess Na2EDTA with Ca2+ or Cu2+. Problem: colour of of Cr3+/EDTA complex probably impedes use of visual indicators.
Or redox: oxidise Cr3+ to dichromate, titrate with Mohr's Salt (Fe2+) to Fe3+/Cr3+... Oh, and add excess KI to the dichromate, oxidising the iodide to
iodine, then titrate with thiosulphate.
[Edited on 26-8-2012 by blogfast25]
[Edited on 26-8-2012 by blogfast25]
|
|
watson.fawkes
International Hazard
   
Posts: 2793
Registered: 16-8-2008
Member Is Offline
Mood: No Mood
|
|
The
design is called the "calrod", still used as a trade name, though passed somewhat into generic status. The "ceramic" inside is generally MgO, a tidbit
that took me quite a while to suss out when I first looked for it.
|
|
blogfast25
International Hazard
   
Posts: 10562
Registered: 3-2-2008
Location: Neverland
Member Is Offline
Mood: No Mood
|
|
Quote: Originally posted by watson.fawkes  | The design is called the "calrod", still used as a trade name, though passed somewhat into generic status. The "ceramic" inside is generally MgO, a
tidbit that took me quite a while to suss out when I first looked for it. |
As luck would have it I had two bits of the alu tube lying on the floor and they still contained some of the filler, which I transferred into a test
tube. It looks pale yellow/off white. Adding a cm of water shows that this material wets very badly, even after vigorous shaking/vibrating. The
supernatant liquid showed neutrality with universal indicator paper.
Then about 2 cm of 95 % H2SO4 was added: no sign of dissolution was noted. 10 minutes on a water bath (boiling) and no change. This is not consistent
with MgO, not even calcined MgO.
Wouldn't fine sand be a cheaper solution? That's used in high amp fuses to embed the fuse wire, for instance...
[Edited on 26-8-2012 by blogfast25]
[Edited on 26-8-2012 by blogfast25]
|
|
watson.fawkes
International Hazard
   
Posts: 2793
Registered: 16-8-2008
Member Is Offline
Mood: No Mood
|
|
Quote: Originally posted by blogfast25  | [...]This is not consistent with MgO, not even calcined MgO.
Wouldn't fine sand be a cheaper solution? That's used in high amp fuses to embed the fuse wire, for instance. | I don't want to claim that all calrod-style heating elements use MgO. The original Calrod brand element did (and still do). Just like not all resistance wires are nichrome, I can't imagine that all fillers are MgO, either. Whatever it is they're using, I
imagine it's both cheaper and has shorter service life.
As far as your actual results, I would guess that you're seeing one or both of Fe or Al migration into the filler material, whatever it be, thus
complicating identification. Insofar as I was able to determine, it seems that the choice of MgO was made exactly because it didn't form intermetallic
oxides readily at high temperature, thus preserving mechanical integrity of both the resistance wire and the cladding tube. For example, an Al tube
and SiO2 filler would generate an aluminosilicate, such as mullite, on grain surfaces; think of this as a slow-motion start of a thermite
reaction. On the other hand, I doubt that MgO, in actual practice, would form much spinel (MgAl2O4) in similar circumstances.
|
|
blogfast25
International Hazard
   
Posts: 10562
Registered: 3-2-2008
Location: Neverland
Member Is Offline
Mood: No Mood
|
|
A few observations:
1. That Calrod design uses a coiled resistor. What I recovered is simply straight resistor wire (about 1 mm D) embedded in filler/sleeve
2. The webpage you link to doesn’t mention any filler
3. What temperature do you think such a resistor would get up to in steady state?
4. If high enough Al from the alloy could react with silica, agreed
5. To form such a spinel (MgAl2O4), oxygen must be present because Al(0) → Al(III). In the design I’ve taken apart there is almost none: the
sleeve is filled and capped at both ends.
[Edited on 27-8-2012 by blogfast25]
|
|
watson.fawkes
International Hazard
   
Posts: 2793
Registered: 16-8-2008
Member Is Offline
Mood: No Mood
|
|
From that page, near the end: Quote: | The wire inside a Calrod element is called NiCr (Nichrome resistor) and is the main source of heat. It is encased with MgO (Magnesium Dioxide) that
offers excellent heat transfer properties. | Yeah, I know. MgO isn't a dioxide.
The coiled resistor design is what they're selling now for industrial applications. The original design was (as I understand) for consumer
applications, and did use a single heavy resistance wire. I've got a burnt-out electrical oven element in my junk box I saved; it has the same heavy
wire. Note how much better the terminations are in the industrial product are (from the referenced page) than the consumer version.
As for steady-state temperatures, they easily get to red heat. Ultimate heat is limited by the strength of the materials at heat. Economic limitations
arise from oxidation lifetime of the materials. Note that they're produced with inconel (a class of high-nickel alloys) cladding, which has very good heat heat properties (used in jet turbines, e.g.) as well as good
chemical resistance at those same temperatures.
I believe that spinel formation is limited by thermodynamic considerations more than oxygen availability. That is, Al won't much reduce MgO, the other
source of oxygen. It's why SiO2 isn't a great refractory packing material for this application, because its thermodynamics are more
favorable for reaction.
(Aside: Oxygen is fairly mobile at refractory temperatures. It will diffuse through many ceramics; there are even conductive ceramics at these
temperatures where O2- is a majority current carrier. Admittedly in the present case that would mean oxygen diffusion through red-hot metal
for it to be an oxygen source; it would react first. I say this to illustrate my caution about thinking about refractory reactions. They don't always
act as they might seem at first.)
As to what your packing actually is, there are a number of candidates. Alumina would be adequate. Titania, perhaps as crude rutile, might be present,
though I don't know how it would be economical, unless it were otherwise a waste product. Any material might have some silica present as an admixture.
It's conceivable there are some fluxing components, such as calcium, to act as binder.
|
|
LanthanumK
Hazard to Others
 
Posts: 298
Registered: 20-5-2011
Location: New Jersey
Member Is Offline
Mood: No Mood
|
|
I have had a similar experience with heating elements. I extracted some coils from a broken hair dryer and they turned out to be kanthal, not
nichrome.
hibernating...
|
|
blogfast25
International Hazard
   
Posts: 10562
Registered: 3-2-2008
Location: Neverland
Member Is Offline
Mood: No Mood
|
|
Thanks, LaK.
And a rather crude test for Al tested negative. Here’s what I did.
Yesterday I’d set aside half of the green ‘resistor chloride’ solution. Today to that half about 10 g of KOH dissolved in about 10 ml of water
was added, precipitating the oxides of Fe and Cr (Cr co-precipitates quantitatively with Fe in these circumstances) but at this very high pH
amphoteric Al should stay in solution. After some stirring of the slurry it was filtered and the filtrate ran clear, about 50 ml.
This was neutralised with about 15 ml 36 % HCl and it was acidic by then. I noted no transient precipitation during the neutralisation. Then it was
alkalised again to pH 8 – 9 with strong ammonia. Again no precipitate formed. It appears that Al content of this alloy is low or nil.
Also, it appears the resistor isn’t a continuous length of thick FeCr wire but multiple lengths of about 1 – 1.5 inch joined together by much
thinner wire, coiled over and soldered to each end/beginning of the thicker sections thus connected. Perhaps this design allows better control of
overall resistance and may also increase the ability to bend the element to the application’s shape, without the resistor(s) touching the Al sleeve.
The filler is indeed a powder (not a massive solid as I originally thought) and it’s very tightly packed.
[Edited on 27-8-2012 by blogfast25]
|
|